Intelligente Formatverstellung für mehr Prozesssicherheit in der pharmazeutischen Produktion
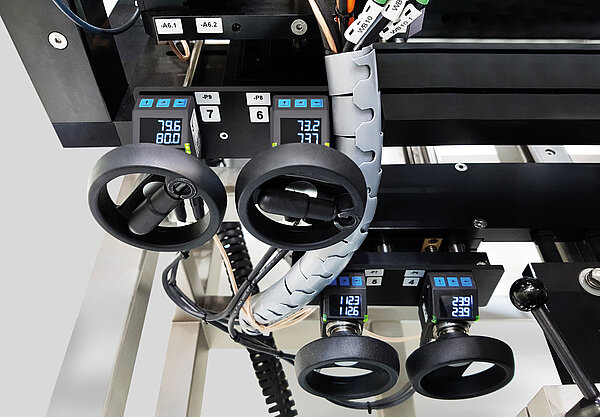
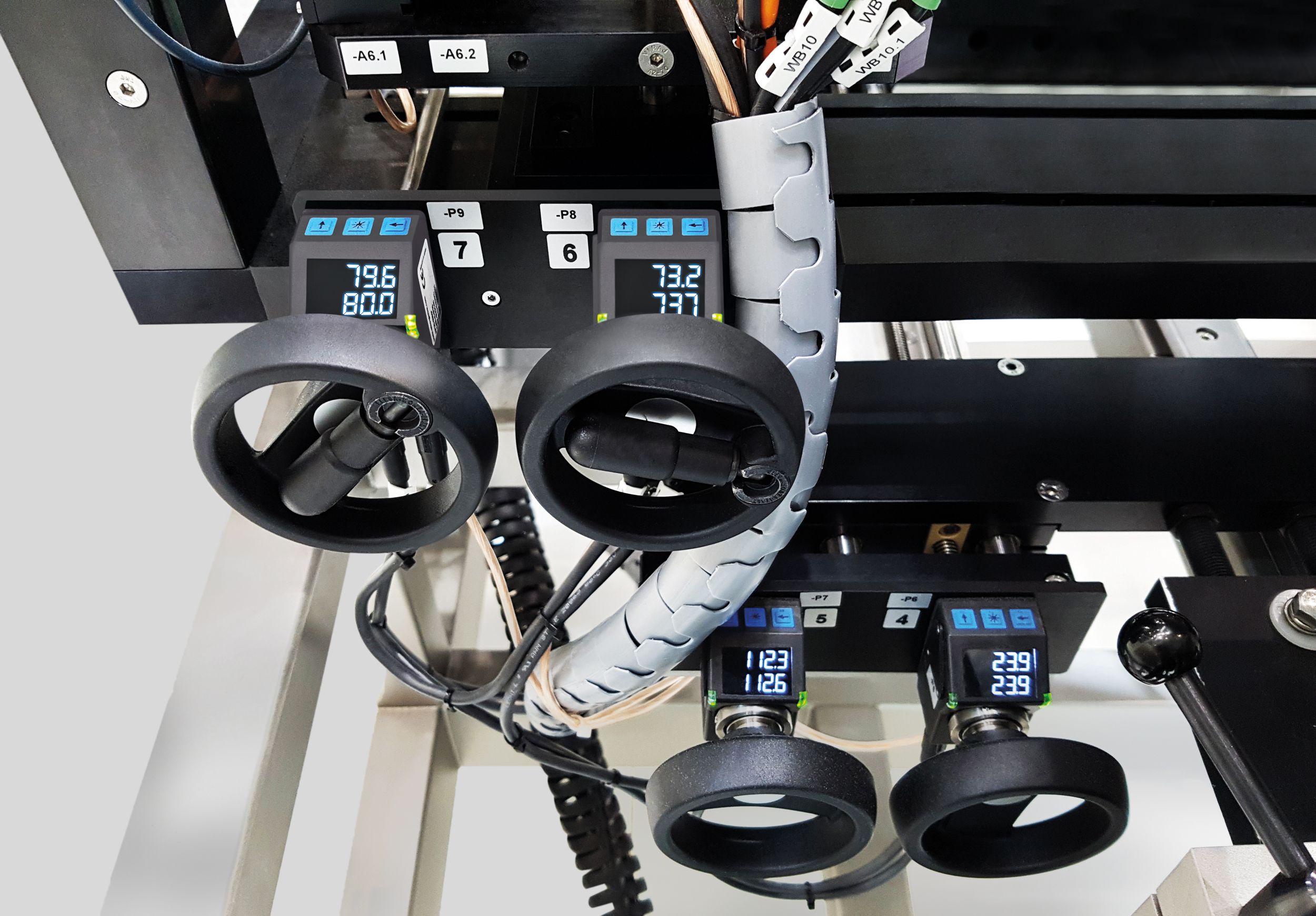
Busfähige, elektronische Positionsanzeigen sorgen bei der Verpackung von Medikamenten für eine prozesssichere und effiziente Umstellung auf unterschiedliche Faltschachtelgrößen
Ein nicht zu unterschätzender Faktor bei der Verbesserung der Anlagenverfügbarkeit ist die Optimierung der Umrüstzeiten bei Produktwechseln, bei der sogenannten Formatverstellung. Hier gibt es verschiedene Möglichkeiten eines intelligenten Formatwechsels, der auf den Centerlining-Gedanken optimierter Einstellungen einzahlt: von einer einfachen rein mechanischen Lösung für einzelne Verstellpunkte bis hin zu vollautomatisierten Positioniersystemen für die gesamte Anlage.
Was Formatverstellung bedeutet
Formatverstellung ist überall in der Herstellung von pharmazeutischen Produkten gegenwärtig. Ob bei Verpackung, Kennzeichnung oder Inspektion: Von Format spricht man, wenn ein neues Maß für ein neues Produkt an einer Maschine eingestellt wird. Nicht erst durch die Automatisierung ist bei jeder Maschine eine Umstellung der Achsen erforderlich, sobald das Produkt bzw. seine Maße verändert werden. Eine Formatverstellung kann dabei sowohl händisch über eine Kurbel erfolgen als auch vollautomatisiert. Je individueller die Anforderungen ausfallen, desto mehr kommt es auf eine intelligente, effiziente Formatverstellung an.
Die gängigste Variante der Formatverstellung ist die Spindelverstellung, z. B. bei Verpackungs- und Etikettiermaschinen. Das Format bzw. die Achse der Maschine wird über die Drehbewegung einer Spindel verstellt. Diese kann händisch über eine Kurbel oder ein Handrad erfolgen oder vollautomatisiert über einen Stellmotor.
Dort, wo keine Spindel zur Verfügung steht, kommt eine Linearführung zum Einsatz. Dabei wird ein Schlitten über eine Schiene geschoben und über diese mechanische Konstruktion die neue Position eingestellt. Hierzu ist bei der manuellen Verstellung viel Fingerspitzengefühl vonnöten, um eine korrekte Einstellung zu erreichen.
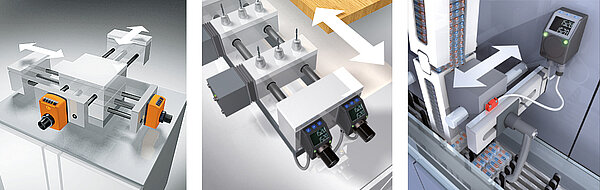
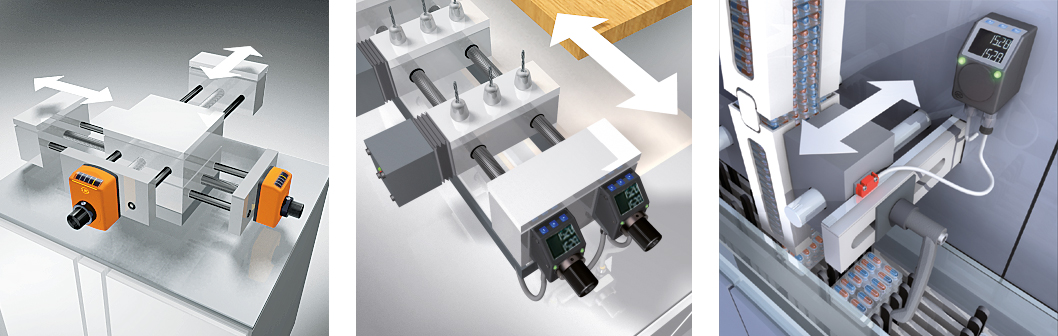
Schematische Darstellung von händischer Formatverstellung über mechanisch-digitale Positionsanzeigen, schematische Darstellung von händischer Formatverstellung über busfähige, elektronische Positionsanzeigen, chematische Darstellung von händischer Formatverstellung über busfähige, elektronische Positionsanzeigen an Linearführungen
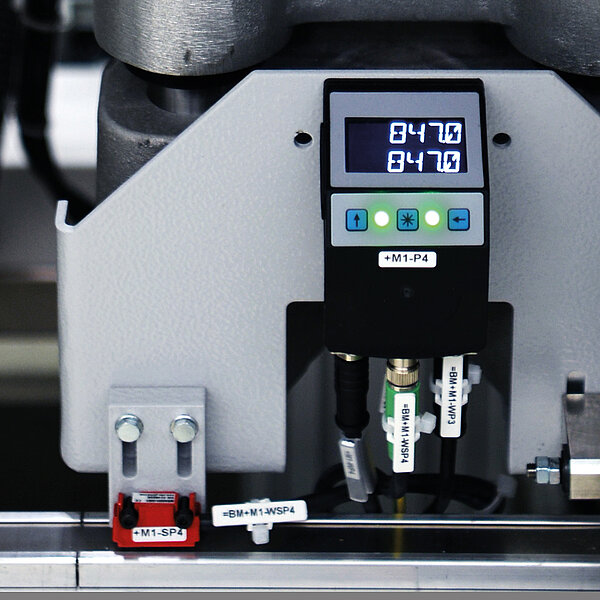
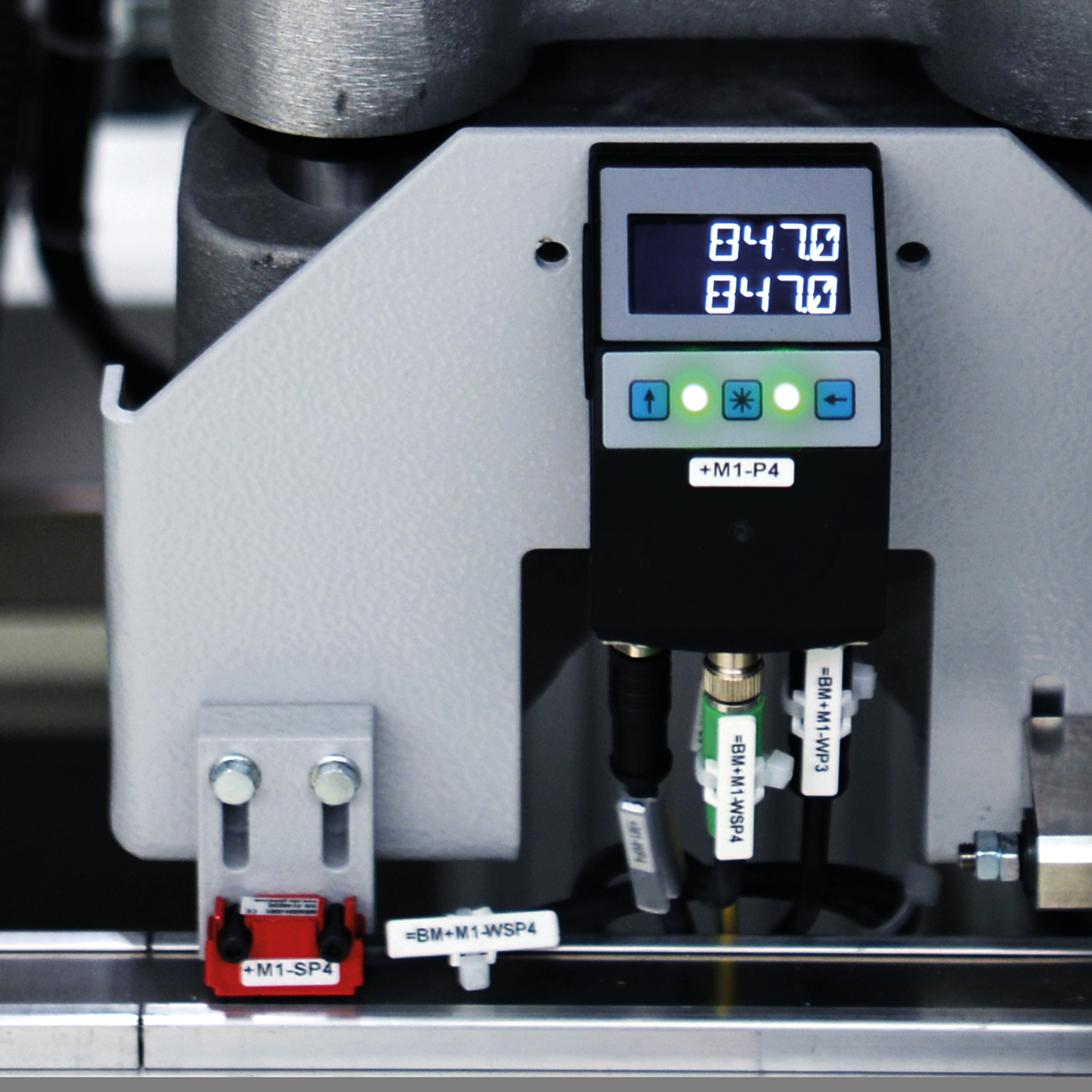
Händische Formatverstellung über busfähige, elektronische Positionsanzeigen an Linearführungen © SIKO GmbH © SIKO GmbH
Beim Formatteilwechsel geht es nicht mehr um eine reine Verstellung von Achsen, sondern hierbei werden Formatteile, also einzelne Werkzeuge oder Maschinenteile, ausgetauscht. Um diesen manuellen Wechsel korrekt durchzuführen, können Überwachungslösungen integriert werden.
Nutzen einer optimierten Formatverstellung
Die Veränderung der Einstellungen einer Maschine birgt immer gewisse Risiken, dabei fehlerhaft vorzugehen. Mit einer optimierten Formatverstellung in punkto Überwachung oder gar Automatisierung lässt sich dieses Risiko ausschließen und besser auf flexible Anforderungen an die Produktionsprozesse reagieren.
Mit der Optimierung der Formatverstellung soll zum einen die Wiederholgenauigkeit erhöht werden. Ein Produkt soll nach einem Wechsel auch bei erneuter Herstellung wieder in gleicher Form und Qualität vorliegen – ein entscheidendes Kriterium bei der Herstellung von Arzneien.
Ein Effekt, der aus der Optimierung der Geschwindigkeit bei den Rüstzeiten resultiert, ist eine signifikante Kostenreduktion. Sie macht sich am stärksten bei überwachter und vollautomatischer Formatverstellung bemerkbar.
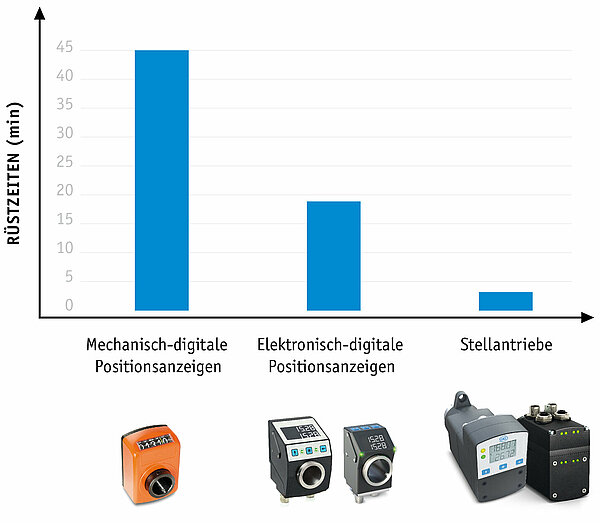

Umso häufiger Formate verstellt werden müssen und umso qualitativ anspruchsvoller die Produktion ist, desto sinnvoller ist der Einsatz von überwachten oder automatisierten Positioniergeräten
Neben Reproduzierbarkeit und Kostenreduktion durch Geschwindigkeit ist eine Erhöhung der Prozesssicherheit ein weiteres Argument für eine Optimierung der Formatverstellung. Bei der überwachten Formatverstellung wird durch LED-Leuchten ein klarer Positionsstatus angezeigt, Grün bedeutet „Position korrekt“, Rot signalisiert „Position nicht korrekt“. Damit besteht die Möglichkeit, die Maschine so zu programmieren, dass sie erst dann die Produktion wieder aufnimmt, wenn alle Positionen korrekt eingestellt sind.
Erhöhte Sicherheit bei kritischen Applikationen
Bei Anwendungen im pharmazeutischen Bereich muss hundertprozentig sichergestellt sein, dass nach der Formatverstellung die korrekte Position erreicht ist – unabhängig davon, ob dies einmal in der Woche oder stündlich geschieht. Hier ist eine überwachte Formatverstellung unerlässlich. Beispielsweise werden bei Maschinen Verpackungsgrößen für Medikamente eingestellt. Dazu muss die Kennzeichnung der Medikamente entsprechend der neuen Verpackung nachgeführt werden, damit eine eindeutige Rückverfolgbarkeit des Produktionsprozesses sichergestellt ist. All diese Aspekte werden über eine Formateinstellung einjustiert.
Eine weitere beispielhafte Anwendung ist die Höhenverstellung für eine Inspektionskamera. Die Position der Kamera muss auf verschiedene Produkthöhen abgestimmt sein, damit eine Inspektion mit 100-prozentiger Sicherheit funktionieren kann.
Manuelle Formatverstellung
Die manuelle Formatverstellung ist prädestiniert für Basismaschinen mit seltenen Formatverstellungen. Es kommen mechanisch-digitale oder elektronische Positionsanzeigen zum Einsatz, die preiswert und zuverlässig die Positionierung feststellen.
In jeder Positionsanzeige befindet sich als Kernelement ein Messsystem, mit dem die Position aufgenommen wird. Das Messsystem verfügt über eine hohe Genauigkeit, typischerweise mit einer Toleranz von ca. ±0.5 Grad bezogen auf die Drehbewegung an der Verstelleinheit. Außerdem bietet eine Positionsanzeige kontrollierbare digitale Anzeigewerte.
Neben dem Messsystem beinhaltet eine Positionsanzeige auch ein Anzeigedisplay. Eine Variante sind die mechanisch-digitalen Positionsanzeigen, die die Werte in Dezimalstellen in Zehnerpotenzen in Form von Zahlenrollen darstellen. Daher rührt die Bezeichnung „digital“, obwohl es sich nicht um elektronische Anzeigen handelt. Elektronische Positionsanzeigen dagegen verfügen über ein LCD-Display. Wenn es um überwachte Formatverstellung geht, kommen Versionen zum Einsatz, die zusätzlich den Soll-Wert in der zweiten Anzeigezeile ausweisen
Absolutes Messprinzip und Kalibrierung
Die Positionsanzeigen arbeiten nach einem absoluten Messprinzip, das nicht ständig referenziert werden muss, d.h. die Anzeige erfasst auch im stromlosen Zustand Bewegungen an der Verstelleinheit. Bei den elektronischen Positionsanzeigen – entweder als Stand-alone oder vernetzt – geschieht dies über eine Batterie, d. h. diese arbeiten nach einem absoluten Messsystem, das batteriegepuffert ist und nur einmalig referenziert werden muss.
Auflösung und Genauigkeit
Mit der Auflösung wird der kleinste ablesbare Messschritt angegeben, den die Anzeige bietet; bei den elektronischen Anzeigen mit Sollwertvorgabe sind es beispielsweise 720 Inkremente pro Umdrehung, wodurch eine hohe Reproduzierbarkeit gewährleistet ist.
Mechanisch-digitale Positionsanzeigen
Die Positionswerte lassen sich mit hoher Präzision erfassen und werden gut ablesbar dargestellt. Über ein integriertes Getriebe wird der Anzeigewert pro Umdrehung für die jeweils geforderte Spindelsteigung passend ausgelegt. Die Besonderheit der mechanischen Positionsanzeigen ist ihre jeweilige ausschließliche Eignung für eine bestimmte Applikation. Für eine Anwendung mit einer bestimmten Spindelsteigung in einer gewünschten Auflösung wird eine spezifische Gerätevariante konfiguriert.
Elektronische Positionsanzeigen LCD stand-alone
Der entscheidende Vorteil elektronischer Positionsanzeigen gegenüber den mechanisch-digitalen ist die freie Programmierbarkeit für eine flexible Nutzung. Eine Vielzahl von Parametern lässt sich über die Positionsanzeige frei konfigurieren: die Spindelsteigung, die Kommastellen, die Drehrichtung, die Einbaulage, auch die Nutzung im Winkelmodus.
Im Vergleich mit den mechanisch-digitalen Positionsanzeigen können mit den elektronischen Anzeigen noch höhere Auflösungen realisiert werden. Bei den mechanischen ist die Getriebeübersetzung begrenzt. Mit den elektronischen Anzeigen lassen sich dagegen bis zu. 3.600 Zählschritte pro Umdrehung realisieren. Eine Einteilung in Zehntelgrad ist damit ohne weiteres möglich. Positiv bei der Abwägung zwischen mechanischen oder elektronischen Positionsanzeigen ist die Anbaukompatibilität zwischen beiden, sodass eine Umrüstung oder Erweiterung unproblematisch ist.
Überwachte Formatverstellung mit elektronischen Positionsanzeigen
Für eine überwachte Formatverstellung kommen elektronische Positionsanzeigen mit Sollwertvorgabe und Buskommunikation zum Einsatz. Im busgesteuerten Betrieb wird der Austausch von Soll-Werten und Ist-Werten zwischen den einzelnen absoluten Positionsanzeigen und einer übergeordneten Steuereinheit möglich.
Grundanforderungen für die Prozesssicherheit
Während bei der manuellen Formatverstellung die Anforderung der Reproduzierbarkeit im Vordergrund steht, geht es bei der überwachten Formatverstellung vor allem um Prozesssicherheit. Dank der Busintegration der Positionsanzeigen wird diese zentral über die Maschinensteuerung (SPS) erreicht. Die SPS ist das führende Element, das Soll-Werte an die Positionsanzeigen sendet und die gemessenen Ist-Werte ausliest. Anhand des übermittelten Positionsstatus gibt sie die Gesamtanlage erst nach korrekter Rückmeldung aller manuell eingestellten Spindelpositionen wieder frei, sodass Ausschuss oder Beschädigungen an Maschinenmodulen durch falsch eingerichtete Verstellachsen nicht mehr vorkommen. Auch Maschineneffizienz und Wirtschaftlichkeit der Produktionsanlagen steigen deutlich durch eine überwachte Formatverstellung mit busfähigen elektronischen Positionsanzeigen.
Diese erhalten von der Maschinensteuerung über Feldbus ihre Grundparametrierung und die jeweils aktuell einzustellende Soll-Position. Die Soll-Werte sind in der Rezeptverwaltung innerhalb der Maschinensteuerung hinterlegt, d. h. für jedes zu fertigende Produkt befindet sich in der Rezeptverwaltung ein Rezept mit allen nötigen Soll-Werten, wie z. B. Länge, Höhe, Breite einer Faltschachtel oder Verpackung. Dafür sind verschiedene Verstellpositionen nötig.
Anzeige des Positionsstatus
Die Maschinensteuerung gibt die Sollwerte vor, die an der Positionsanzeige in der zweiten Zeile mit dargestellt werden. Das Besondere bei der überwachten Formatverstellung sind darüber hinaus die beiden LED-Leuchten, die den Positionsstatus mit Grün für „Position korrekt“ und Rot für „Position nicht korrekt“ klar anzeigen.
Die LED-Funktion sowie eine integrierte Pfeilrichtungsanzeige wirken sich auch positiv auf Ergonomie und Bedienerfreundlichkeit aus. Dank der Pfeilrichtungsanzeige wird für den Bediener deutlich, in welche Richtung die Verstellung zu erfolgen hat. Er muss keine Zahlenwerte interpretieren, sondern um die Zielposition zu finden, sind nur die LEDs mit Richtungsanzeige notwendig.
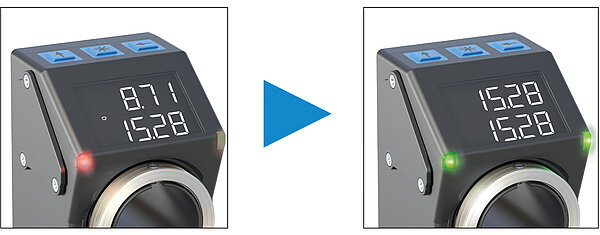
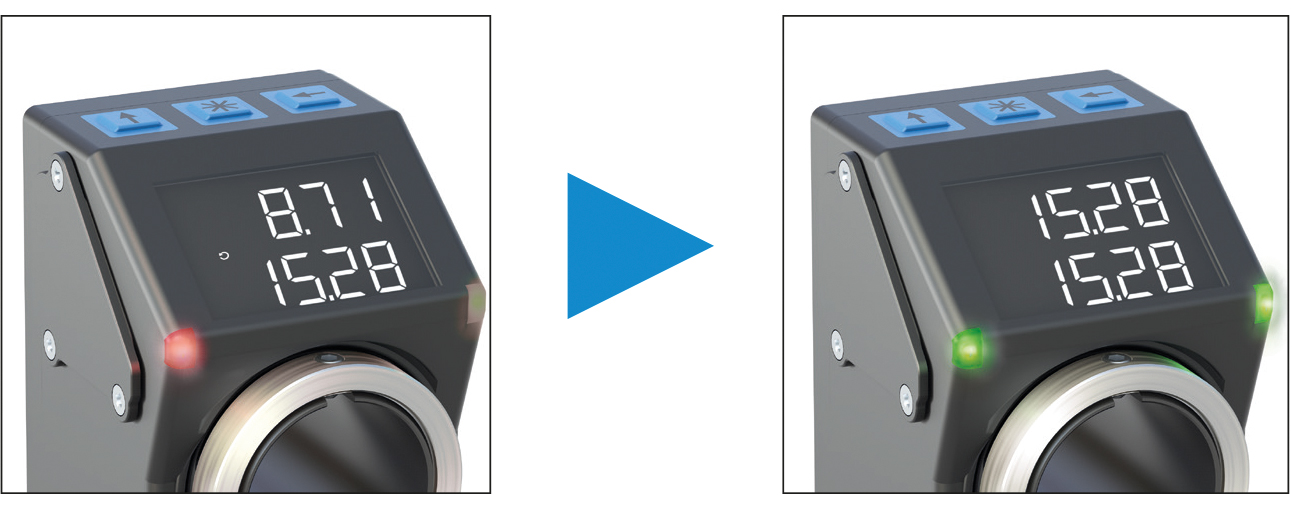
Überwachte Positionsanzeigen visualisieren über Ist- und Sollwertangaben sowie über rote und grüne LED, eindeutig, ob die jeweilige Achse / Spindel korrekt eingestellt ist.
Die freie Parametrierung der vernetzten Positionsanzeige ist ähnlich flexibel wie bei den LCD-Anzeigen. Besonders vorteilhaft ist in diesem Fall, dass die Parametrierung über die Busschnittstelle vorgenommen werden kann und sollte.
Applikationen
Anwendungen für überwachte Formatverstellungen gibt es in den verschiedensten Bereichen des pharmazeutischen Maschinenbaus. Besonders typisch ist die Formatverstellung bei der Einstellung der Verpackungsgrößen für die Kartoniermaschinen sowie bei der Kennzeichnung der Produkte. Im Zuge der europäischen Fälschungsschutzrichtlinie müssen verschreibungspflichtige Medikamente mit einer eindeutigen Kennzeichnung versehen werden, die über sogenannte „Track & Trace“-Systeme erfolgen. Eine überwachte Formatverstellung mit busfähigen elektronischen Positionsanzeigen erhöht die Prozesssicherheit dieser „Track & Trace“-Anlagen, bei denen es u. a. um die Prozesse Drucken, Lesen, Etikettieren und Wiegen geht.
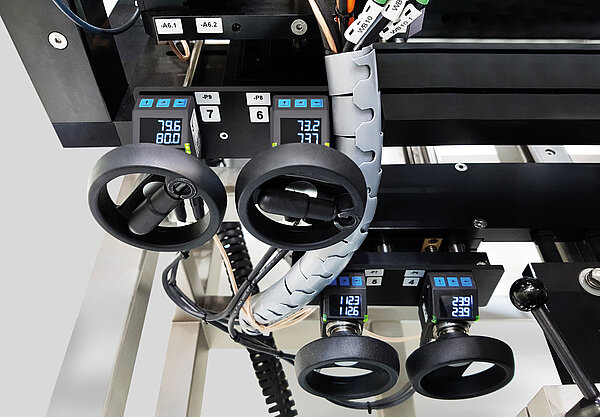
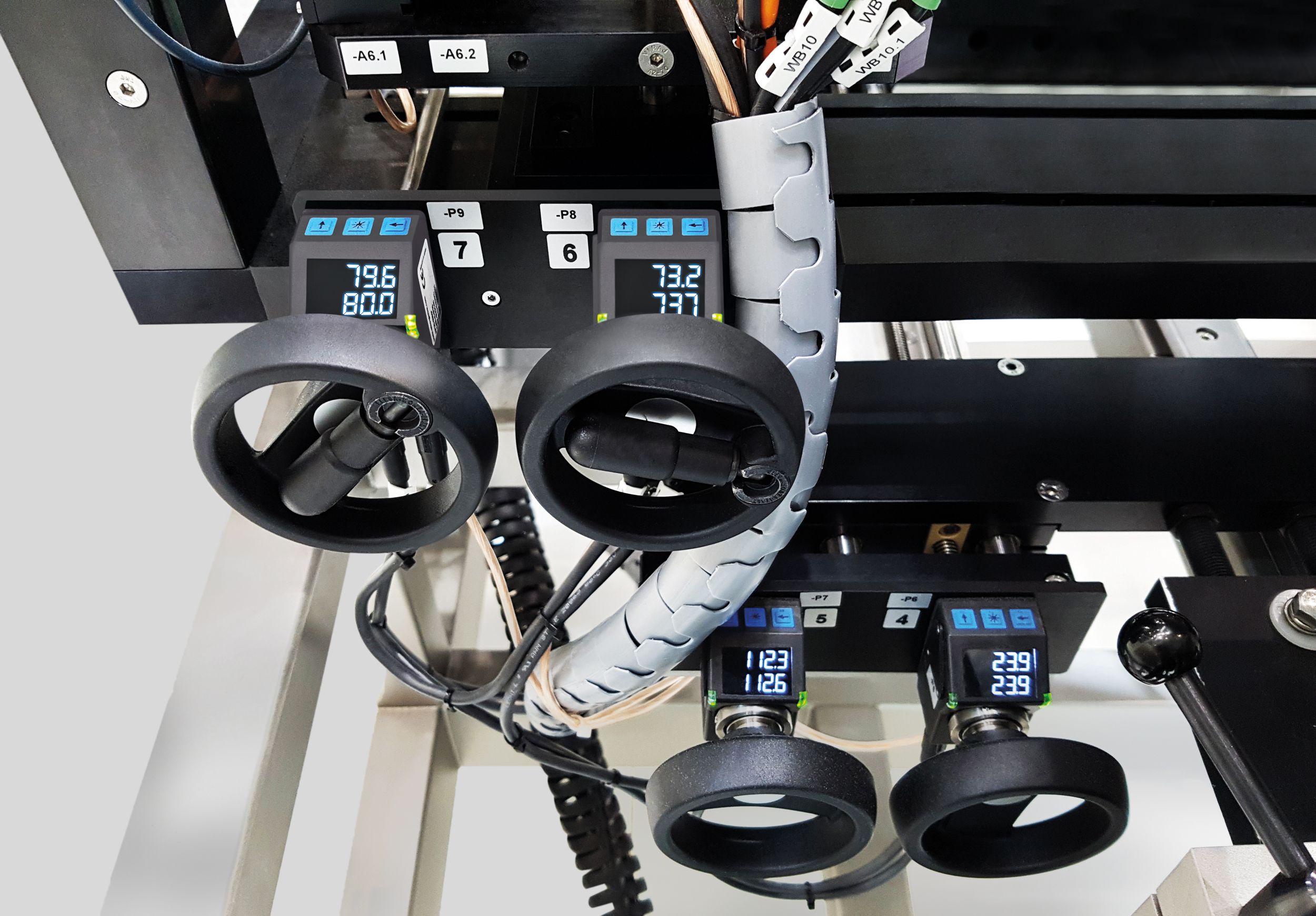
Busfähige, elektronische Positionsanzeigen sorgen bei der Verpackung von Medikamenten für eine prozesssichere und effiziente Umstellung auf unterschiedliche Faltschachtelgrößen
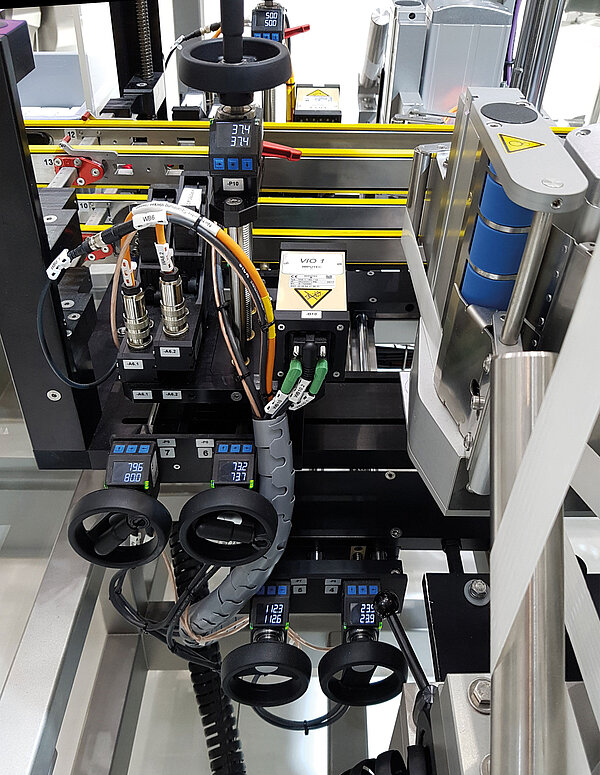
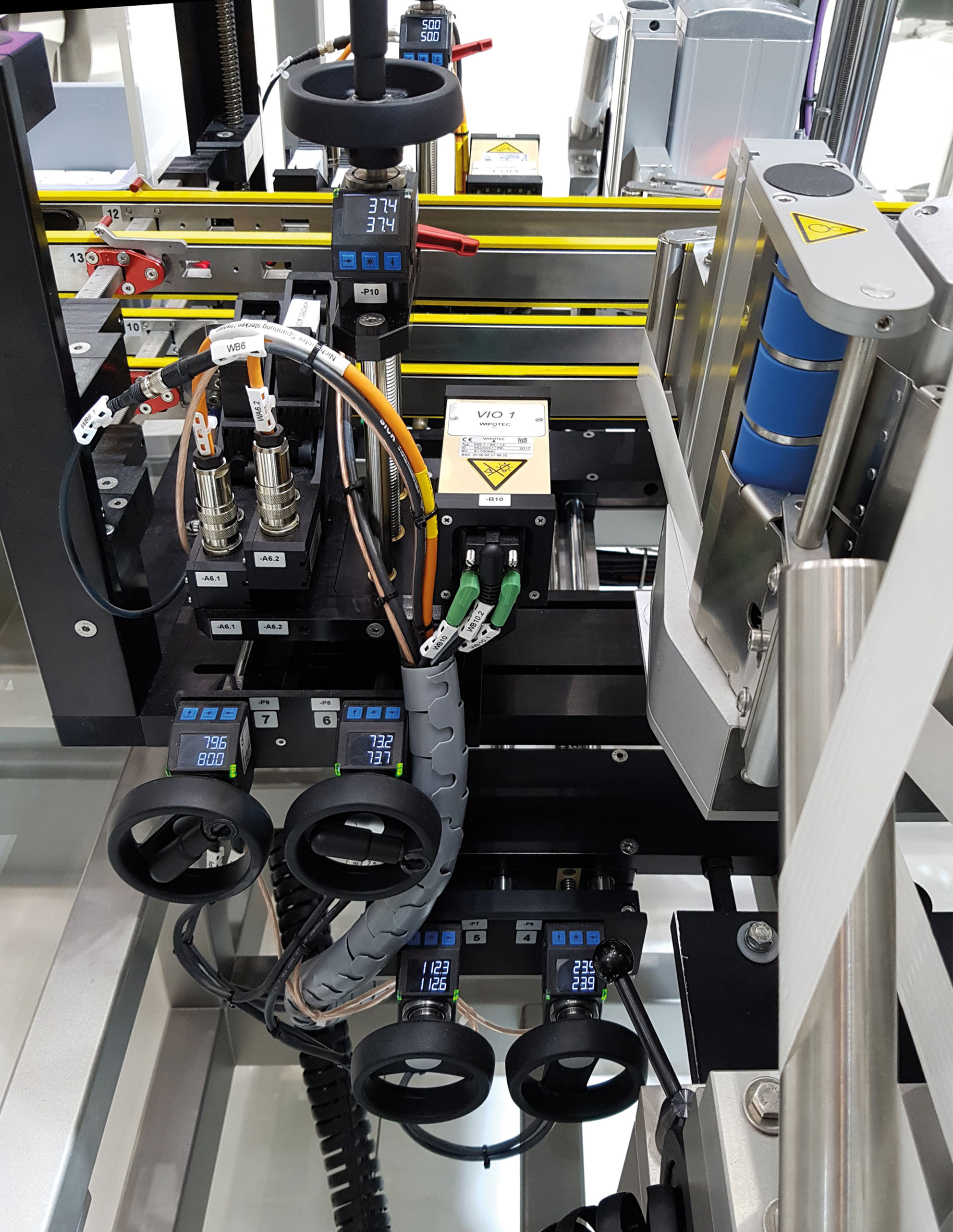
Bei einer „Track & Trace“-Anlage werden die mittleren beiden Positionsanzeigen für die Verstellung des Abstands der Druckköpfe zur Faltschachteloberfläche (unterschiedlicher Breite) eingesetzt. Die unteren beiden Anzeigen helfen bei der Einstellung eines Tamper-Evident-Labellers auf die jeweilige Schachtelbreite
Überwachte Soll-Wert-Anzeigen
Während bei den elektronischen Positionsanzeigen für Spindelverstellung und Linearschieber die Erfassung des Messwerts einen großen Teil der Funktionalität ausmacht, geht es beim Formatteilwechsel ausschließlich um die Anzeige des reinen Soll-Werts vor Ort. Die Prozesssicherheit hängt hier allerdings stark vom jeweiligen Bediener ab, der das richtige Formatteil einsetzen und per Tastendruck quittieren muss.
Automatische Formatverstellung
Der nächste Schritt über die Überwachung der Formatverstellung hinaus ist die vollständige Automatisierung der Verstellungen über Kompaktstellantriebe ohne manuelle Eingriffe. Es sprechen zwei Gründe für die Automatisierung: Zum einen verringern sich die Umrüstzeiten deutlich, was gerade bei häufigen Produktwechseln interessant ist. Zum anderen gibt es häufig Achsen, die schwer zugänglich sind, die beispielsweise nur über eine Leiter oder nur durch Entfernen von Verkleidungsteilen zu erreichen sind, sodass die automatische Verstellung eine Erleichterung bedeutet.
Aufbau eines Stellantriebs
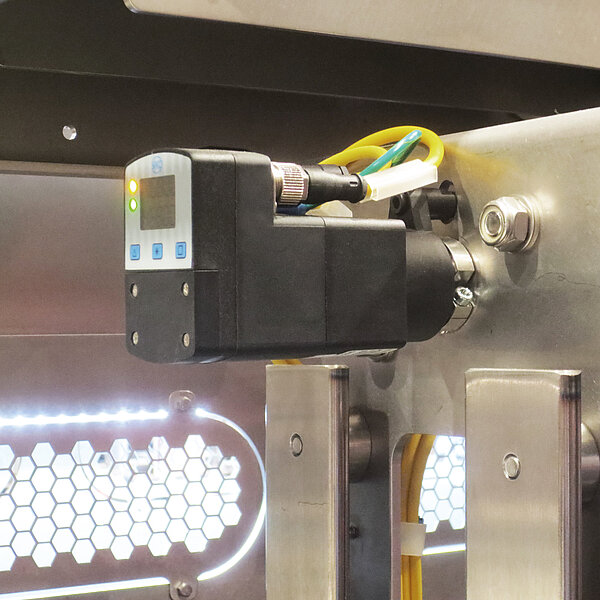
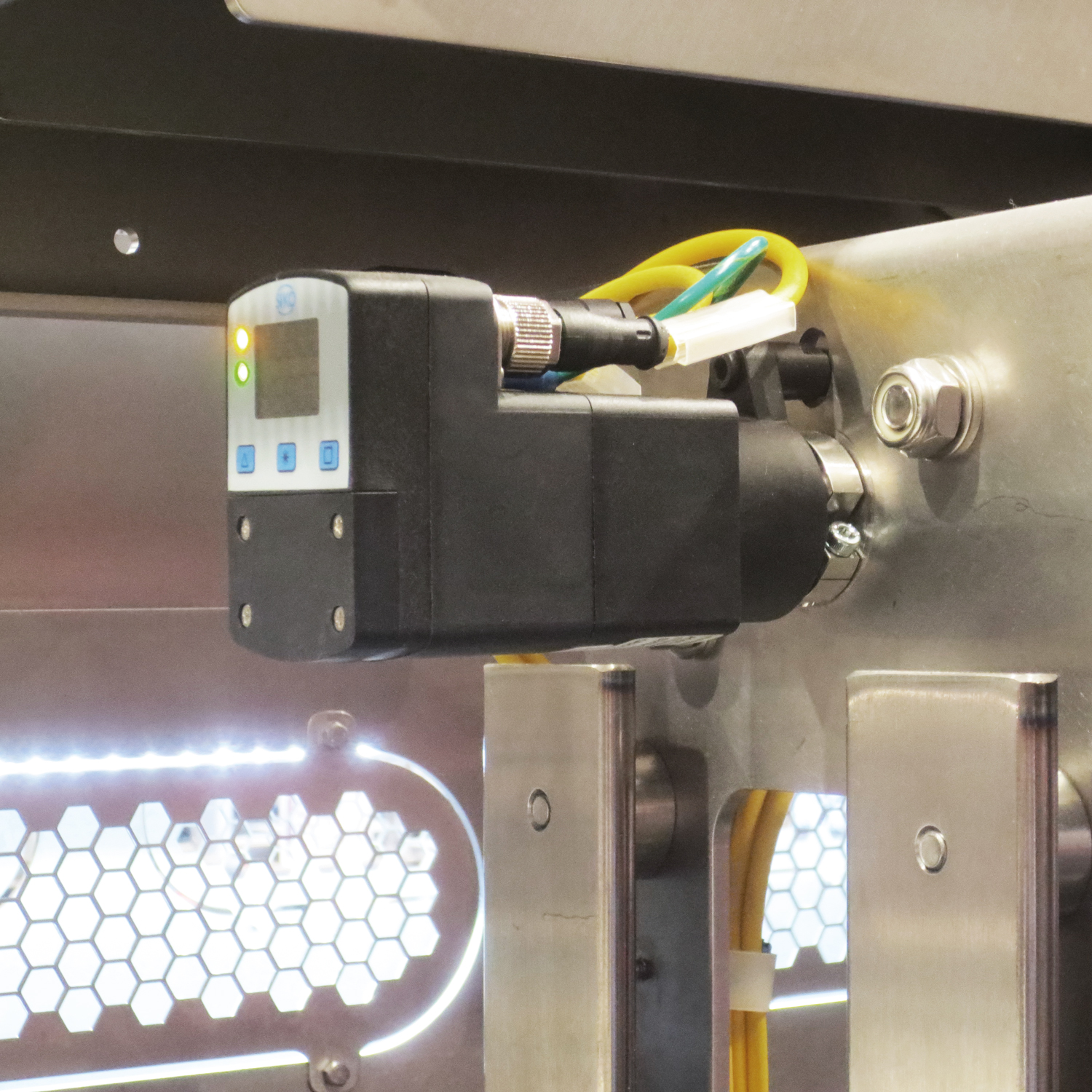
Ein kompakter Stellantrieb hat, trotz dessen minimalen Ausmaße, alle relevanten Komponenten integriert und ist auch für enge oder schwer zugängliche Bauräume geeignet
Die grundlegende Idee eines Stellantriebs ist die hochintegrierte Bauweise, durch die „alle“ Komponenten im Gerät selbst vorhanden sind: der bürstenlose Gleichstrommotor (der verschleißfrei ist), ein spielarmes und leistungsstarkes Getriebe sowie Positionsgeber und Leistungs- und Steuerungselektronik. So kann der Stellantrieb direkt mit der Steuerung verbunden werden. Durch die integrierte Hohlwelle ist auch der Stellantrieb einfach an die vorhandene Spindel zu adaptieren.
Durch diverse Standardschnittstellen ist eine direkte Kommunikation mit der übergeordneten Maschinensteuerung möglich. Diese fungiert als Leitstelle, die dem Antrieb die Soll-Werte und auch den Startbefehl vorgibt. Die Regelung der vollautomatisierten Positionierung hinsichtlich u. a. Zielwert und Geschwindigkeit erfolgt jedoch innerhalb des Antriebs.
Unterschiedliche Leistungsklassen
Die Bandbreite von Formatverstellungen ist relativ groß. Es beginnt bei einer einfachen Feinjustage, wo zum Beispiel bei einem Faltschachtelmagazin im Verpackungsprozess über einen kleinen Drehknopf bei der manuellen Verstellung eine Feinjustage durchgeführt wird. Hierbei werden nur geringe Drehmomente benötigt. Daher können kleine Antriebe mit einem geringen Leistungsbedarf eingesetzt werden.
Das andere Extrem zeigt sich z. B. bei Verpackungsmaschinen, wo komplette Zuführsysteme für Kartonagen je nach Verpackungsgröße in der Breite eingestellt werden müssen, also ganze Maschinenaggregate bewegt werden. Hierzu werden relativ hohe Drehmomente benötigt.
Ein typischer Anwendungsfall im pharmazeutischen Verpackungsbereich ist der sogenannte Kartonagenaufrichter, durch den die gefalteten Kartonagen zu Boxen aufgerichtet werden. Für diese Applikation eignen sich Antriebe aus dem mittleren Leistungsbereich zwischen 50 und 70 Watt.
Prozessdatenaustausch
Die Stellantriebe arbeiten prinzipiell in zwei verschiedenen Modi, die als Standardbetriebsarten gelten: Positioniermodus und Drehzahlmodus. Beim Positioniermodus wird der Soll-Wert von der Steuerung an den Antrieb übertragen. Dieser regelt dann selbstständig mit der vorab von der Steuerung geforderten Geschwindigkeit in die gewünschte Position, bis er dort ankommt. Beim Drehzahlmodus gibt die Steuerung nur eine Geschwindigkeit und Richtung vor und überwacht dann permanent den Ist-Wert, bis die gewünschte Position erreicht ist. Wenn der Antrieb in die Nähe der Position kommt, regelt die Steuerung die Geschwindigkeit bzw. die Drehzahl herunter.
Eine wichtige Sicherungsfunktion ist, dass die Maschine erst dann wieder funktioniert, wenn alle Achsen bzw. Antriebe ihre jeweilige Position gefunden haben. Wenn die Position erreicht ist, wird im Telegramm – dem Kommunikationsaustausch zur Steuerung – ein entsprechendes Bit als Bestätigung der Position gesetzt. Zusätzlich könnte die Steuerung auch noch den Ist-Wert am Antrieb zurücklesen und erneut mit dem Soll-Wert abgleichen. Stimmen beide überein, kann die Steuerung die Wiederaufnahme der Produktion veranlassen.
Flexibel durch Parametrierung
Um den Antrieb an die jeweilige Anwendung optimal anpassen zu können, lassen sich über die Busschnittstelle zahlreiche Parameter festlegen. Der einfachste Parameter ist die Festlegung der Verstellung in Millimeter. Dazu muss der Programmierer wissen, wie viel linearer Weg pro Umdrehung an der Achse bewegt wird. Dieser Parameter kann im Antrieb hinterlegt werden.
Darüber hinaus lassen sich auch Beschleunigungs- und Bremsrampen programmieren, sodass festgelegt wird, wie schnell der Antrieb beschleunigt und wie schnell oder langsam er wieder abbremst. Das ist wichtig für eine genaue Positionierung, damit er über die gewünschte Position nicht hinausfährt. Ebenfalls lässt sich als Parameter auch der Maximalstrom einstellen, um ein gewisses Drehmoment zu limitieren. So können bestimmte Sicherheitsvorkehrungen gewährleistet werden.
Predictive Maintenance
Hinter diesem Aspekt verbirgt sich die Diagnosefähigkeit, die in den Stellantrieben steckt. Über diverse Parameter des Antriebs lassen sich Rückschlüsse auf den Betriebszustand sowohl des Antriebs als auch der Anlage an sich ziehen, um so frühzeitig Unregelmäßigkeiten oder Wartungsbedarf zu erkennen. Beispielsweise lassen sich die Stromaufnahme im Motor, die Temperatur oder die Spannungswerte an Steuer- und Laststromkreis überwachen, sodass frühzeitig Maßnahmen bei Überschreiten der Werte eingeleitet werden können.
Netzwerkintegration zur intelligenten Formatverstellung
Bei der Netzwerkintegration ist bei der Wahl der Schnittstellen eine gewisse Kompatibilität zu der bereits vorhandenen Maschinensteuerung gefordert. Bei einer Siemens-Steuerung beispielsweise ist es am einfachsten, ein Gerät mit Profibus- oder Profinet-Schnittstelle zu integrieren. RS485 und CAN sind seit langem etablierte, kostengünstige serielle Schnittstellen. Damit können eine Vielzahl von Feldgeräten mit einer relativ hohen Geschwindigkeit über große Strecken vernetzt werden.
IO-Link ist eine serielle, bidirektionale Punkt-zu-Punkt-Verbindung zur Signalübertragung und Energieversorgung in beliebigen Netzwerken oder Feldbussen. IO-Link hat in den letzten Jahren bereits eine hohe Verbreitung v. a. im europäischen Maschinenbau erreicht. An jeden IO-Link Master werden mehrere, meist bis zu acht, IO-Link-Feldgeräte sternförmig angeschlossen. Die Inbetriebnahme wird durch die Punkt-zu-Punkt Verbindung sehr vereinfacht, da IO-Link-Geräte nicht adressiert werden müssen. Außerdem lässt sich im Fehlerfall die Störung schnell lokalisieren, und sie hat keine Auswirkung auf weitere Feldgeräte.
Bei den modernen Industrial-Ethernet-Schnittstellen liegt eine sehr hohe Reaktionsgeschwindigkeit vor. Es kann eine beliebige Topologie eingesetzt werden, auch ein Ringaufbau ist möglich. Das erhöht die Betriebssicherheit, weil alle Teilnehmer beidseitig erreichbar sind, was besonders bei einer Unterbrechung der Verbindung entscheidend ist. Über die Industrial-Ethernet-Schnittstellen ist ein umfassender Prozess- und Diagnosedaten-Austausch möglich, der auch die Maßnahmen zur „Predictive Maintenance“ unterstützt.
Fazit und Ausblick: Mehr Automatisierung, mehr Daten
Die Anforderungen an die Flexibilität und Verfügbarkeit von Maschinen und Anlagen im Pharmabereich bleiben hoch. Damit wird die Notwendigkeit einer intelligenten Formatverstellung bestehen bleiben. Der Trend in der Medikamentenherstellung geht zu kleineren Chargen und damit verbunden häufigeren Produktwechseln auf den Anlagen. Der Automatisierungsgrad in den Maschinen wird sicher noch weiter zunehmen, auch im Hinblick auf neuere Systeme wie „Track & Trace“, die die Nachverfolgbarkeit von Medikamenten gewährleisten sollen. Unterstützenden Komponenten, durch die Verstellungen zwischen verschiedenen Produktgrößen schnell, kontrolliert und prozesssicher vollzogen werden können, kommt damit eine immer größere Bedeutung zu. Gerade Prozesssicherheit ist in der Herstellung von Arzneien entscheidend. Durch eine überwachte oder automatisierte Formatverstellung kann die Fehleranfälligkeit durch den „Faktor Mensch“ weiter reduziert werden.
Mehr Intelligenz und Konnektivität für Pharma 4.0
Bei der Weiterentwicklung von intelligenten und flexiblen Lösungen für Produktionsanlagen wird den Peripheriebausteinen wie Anzeigen und Stellmotoren eine größere Rolle zukommen. Hilfreich wird es sein, wenn die genannten Komponenten neben den eigentlichen Prozessdaten noch mehr Informationen über den Betriebszustand der Anlage sammeln. Die Anzeigen und Antriebe könnten dann eigenständig Maßnahmen ergreifen, z. B. dass Warnmeldungen abgesetzt werden oder bei einem Antrieb die Leistung reduziert wird, wenn Grenzbereiche überschritten werden. Das Thema Eigendiagnose wird in der Zukunft bei diesen Komponenten noch wichtiger werden. Dies kann bis zur Lebensdauerüberwachung reichen, sodass auch intern Daten gesammelt werden und der Peripheriebaustein sich zu einem Datenlogger entwickelt.