Die industrielle Produktion ist geprägt von einer immer größer werdenden Produktvielfalt, die durch sinkende Losgrößen in der Fertigung abgebildet wird. Je stärker Produkte individualisiert werden müssen, desto mehr steigen die Anforderungen an die Flexibilität von Produktionsanlagen. Es geht um die optimale Anlagenverfügbarkeit und die Reduzierung von Stillstands- und Rüstzeiten bei kleinsten Losgrößen bis hin zur Stückzahl „eins“. Ein nicht zu unterschätzender Faktor bei der Verbesserung der Anlagenverfügbarkeit ist die Optimierung der Umrüstzeiten bei Produktwechseln, bei der sogenannten Formatverstellung.
Nicht zwangsläufig ist dabei eine aufwendige und kostenintensive Automatisierung der gesamten Anlage vonnöten. Vielmehr sollten sämtliche Verstellpunkte gezielt auf ihre Optimierbarkeit überprüft und jede Achse für sich betrachtet mit entsprechenden Positioniersystemen ausgestattet werden. Die Möglichkeiten reichen von einer kostengünstigen, rein mechanischen Lösung bis hin zu Industrie-4.0-fähigen, „smarten“ Positioniersystemen, die miteinander vernetzt sind und untereinander kommunizieren. So können die Produktionsabläufe effizient gestaltet und damit Kosten minimiert werden.
Was Formatverstellung bedeutet
Obgleich ein etwas sperriger Begriff, ist Formatverstellung überall in der Industrie, in jeder Maschine und Branche gegenwärtig. Ob Verpackungs- oder Holzbearbeitungsmaschine: Von Format spricht man, wenn ein neues Maß für ein neues Produkt an einer Maschine eingestellt wird.
Nicht erst durch die Automatisierung ist bei jeder Maschine eine Umstellung der Achsen erforderlich, sobald das herzustellende Produkt bzw. seine Maße verändert werden, um exakt das Produkt liefern zu können, das der Kunde bestellt hat. Eine Formatverstellung kann dabei sowohl händisch über eine Kurbel erfolgen, als auch vollautomatisiert. Je individueller Kundenwünsche ausfallen, desto mehr kommt es auf eine intelligente, hocheffiziente Formatverstellung an.
Wie Formatverstellung umgesetzt wird
Wie die Formatverstellung technisch konkret umgesetzt wird, hängt von der Konstruktion der Maschine oder des Aggregats ab. Dementsprechend lassen sich drei Varianten der Formatverstellung unterscheiden: die Spindelverstellung, die Verstellung über Schieber bzw. Linearführungen und der Formatteilwechsel.
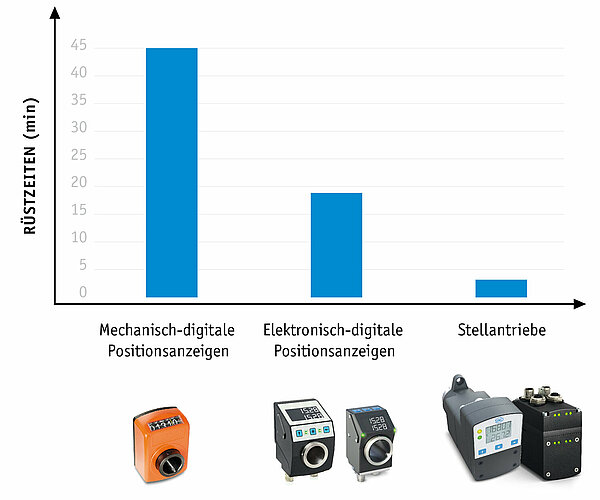
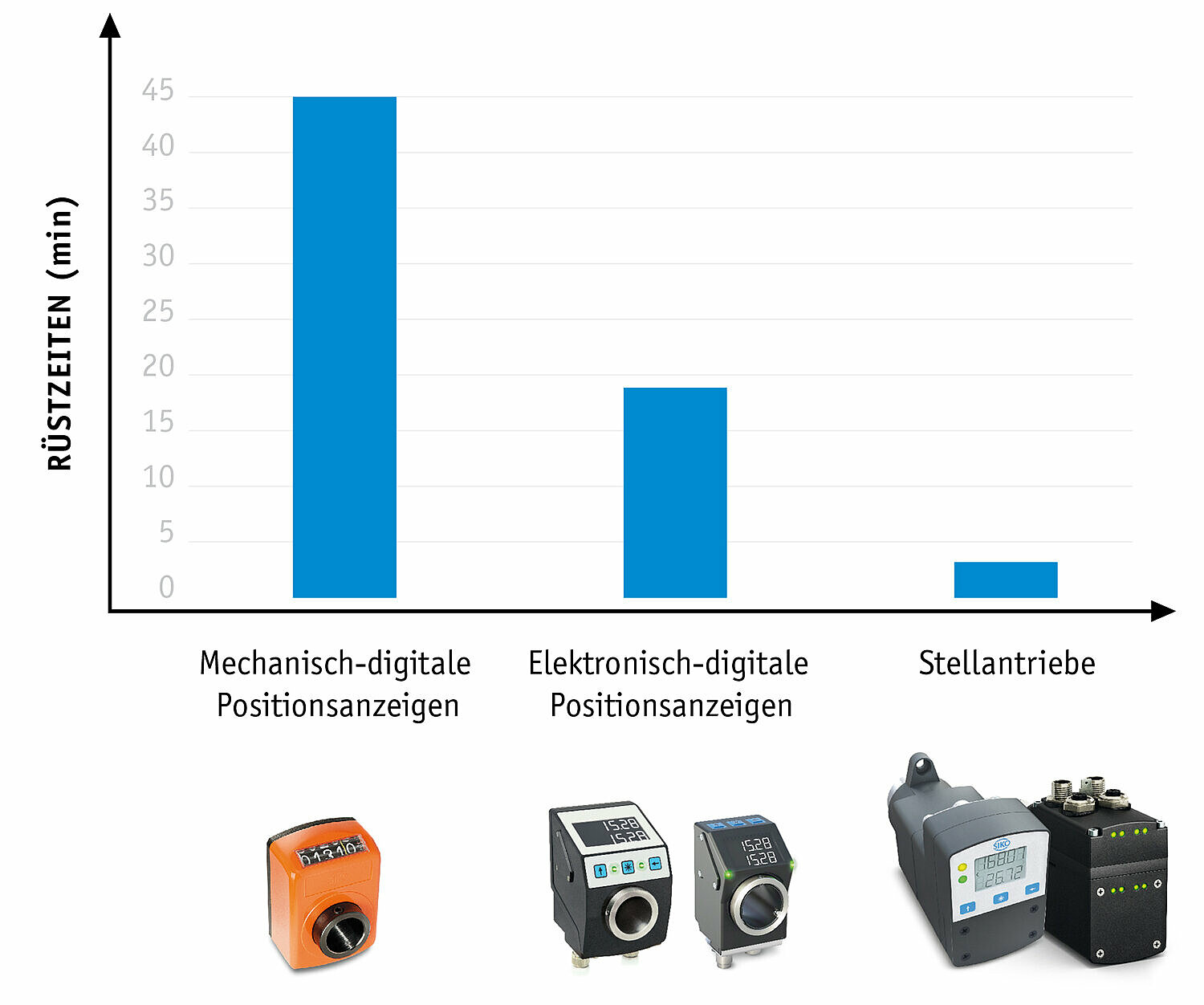
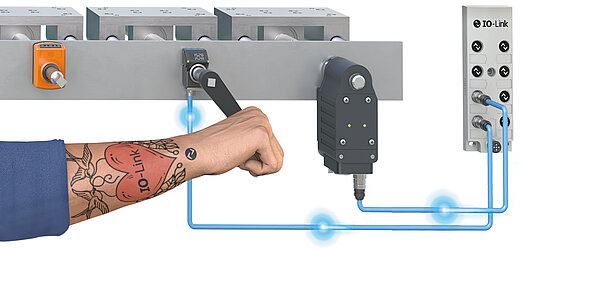
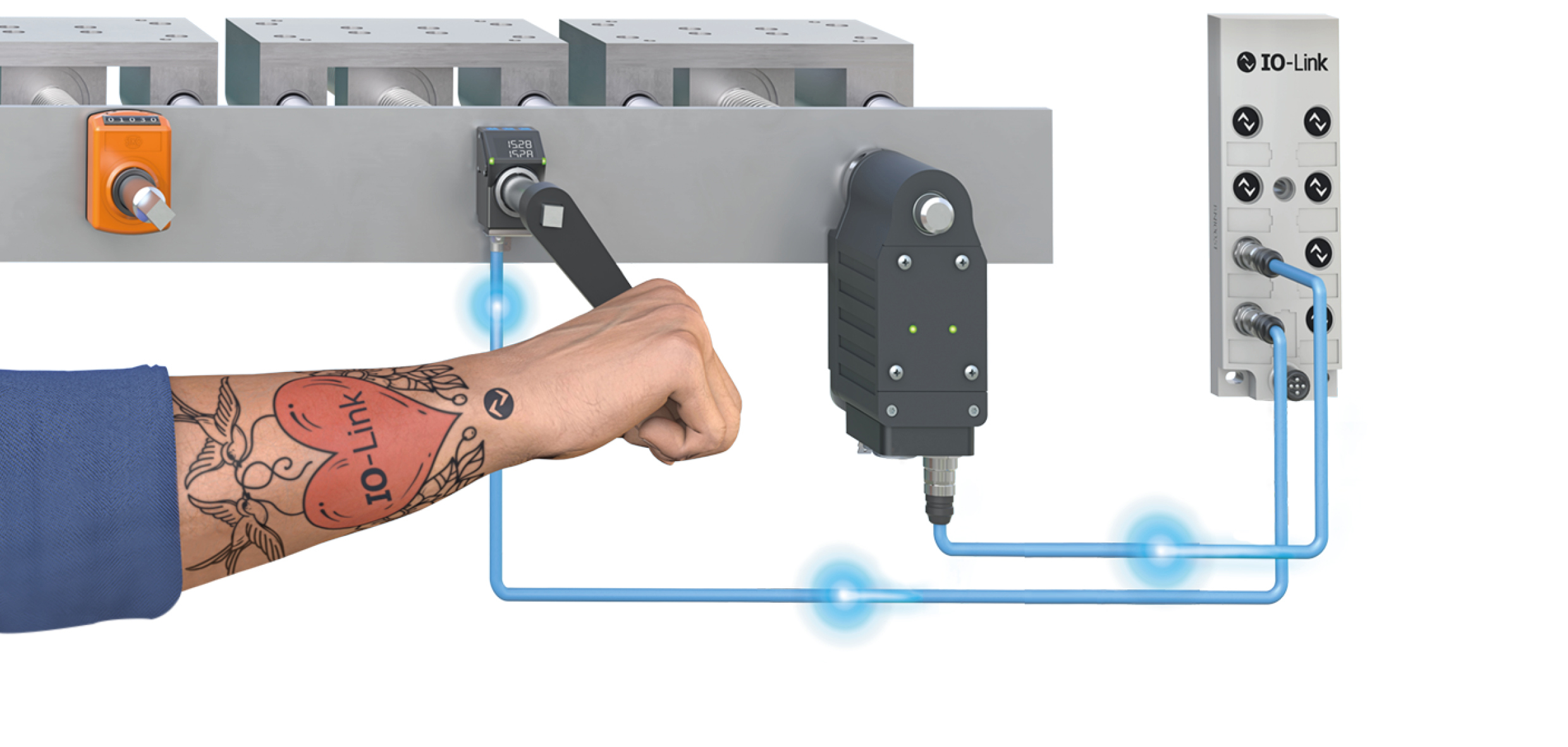
Spindelverstellung
Die Spindelverstellung ist die gängigste Variante der Formatverstellung, z. B. bei Verpackungs-, Holzbearbeitungs- oder auch Druckmaschinen. Das Format bzw. die Achse der Maschine wird über die Drehbewegung einer Spindel verstellt. Diese kann händisch über eine Kurbel oder ein Handrad erfolgen oder vollautomatisiert über einen Stellmotor. Mit der Spindelverstellung ergibt sich eine äußerst feine Justagemöglichkeit, da pro Umdrehung in der Regel nur wenige Millimeter zurückgelegt werden, um das Aggregat neu einzustellen. Im Gegensatz dazu ist es bei einer Linearführung, bei der manuell verschoben wird, deutlich schwieriger, einen Wert so präzise zu fixieren.
Verstellung über Schieber/Linearführungen
Dort, wo keine Spindel zur Formatverstellung zur Verfügung steht, kommt eine Linearführung zum Einsatz. Dabei wird ein Schlitten über eine Stange geschoben und über diese mechanische Konstruktion die neue Position eingestellt. Hierzu ist bei der manuellen Verstellung viel Fingerspitzengefühl vonnöten, um eine korrekte Einstellung zu erreichen.
Eine typische Anwendung für eine lineare Formatverstellung ist eine Kreissäge, bei der der Anschlag für das Holz auf das passende Maß geschoben werden muss, um ein Brett in entsprechender Größe zuschneiden zu können. Bei einer linearen Formatverstellung ist die manuelle Variante gegenüber einer automatisierten Verstellung üblich, da es wesentlich schwieriger und aufwendiger ist, eine Linearbewegung zu automatisieren als eine Drehbewegung. Um eine Linearführung dennoch möglichst präzise verstellen zu können, bietet sich eine überwachte Formatverstellung mithilfe busfähiger Positionsanzeigen an.
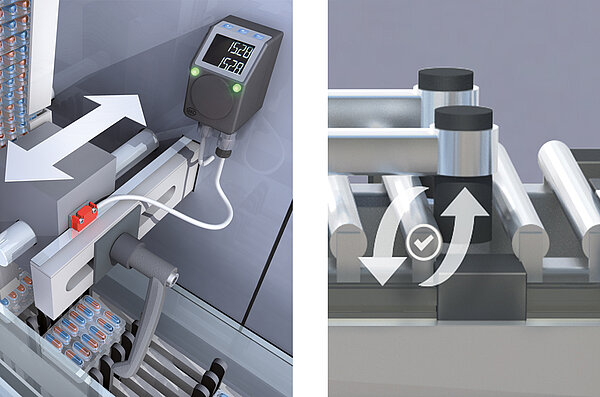
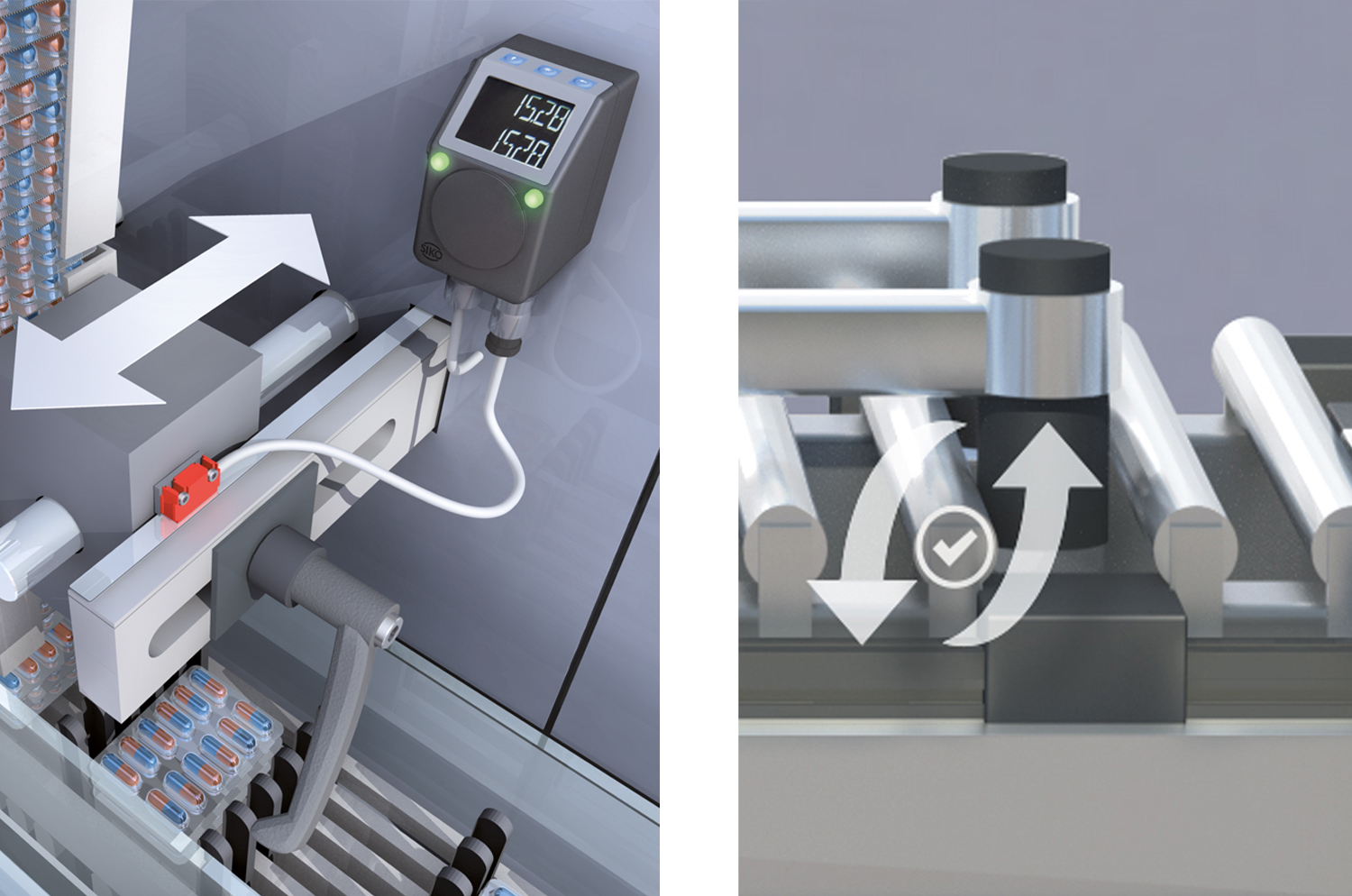
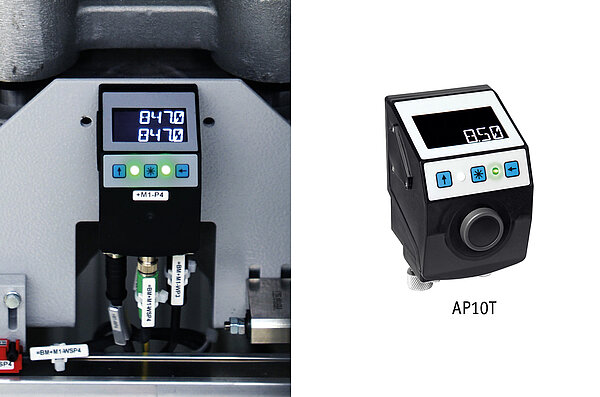
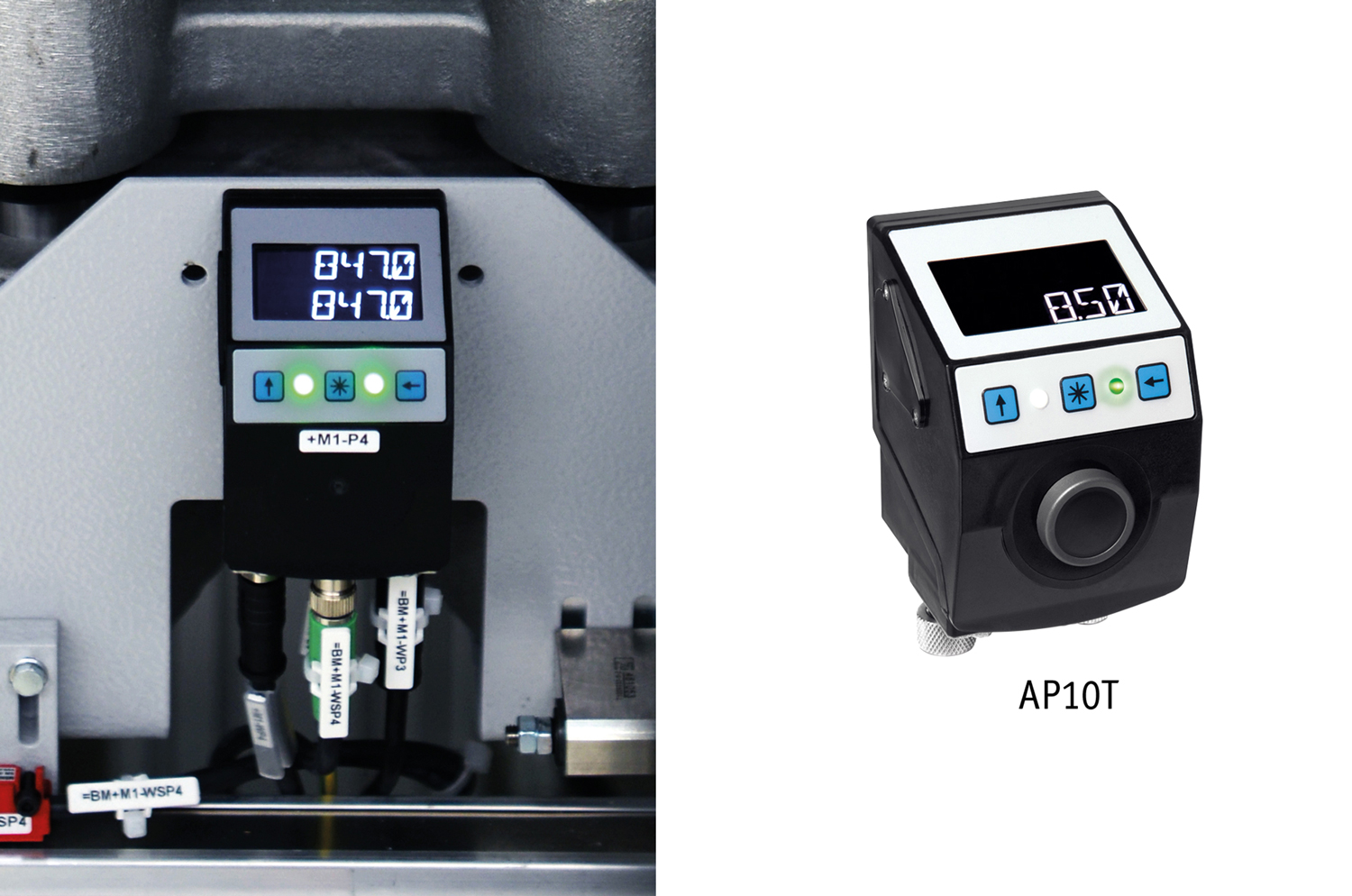
Formatteilwechsel
Beim Formatteilwechsel geht es nicht mehr um eine reine Verstellung von Achsen, sondern hierbei werden Formatteile, also einzelne Werkzeuge oder Maschinenteile als solches ausgetauscht. Um diesen manuellen Wechsel korrekt durchzuführen, stellt SIKO Lösungen zur Überwachung bereit. Ein Formatteilwechsel könnte auch automatisiert durchgeführt werden; hierzu wäre Robotertechnik vonnöten, die jedoch nicht Gegenstand dieses Whitepapers ist.
Nutzen einer optimierten Formatverstellung
Die Veränderung der Einstellungen einer Maschine birgt immer Fehlerpotenzial. Mit einer optimierten Formatverstellung in punkto Überwachung oder gar Automatisierung lässt sich dieses Risiko ausschließen und besser auf flexible Anforderungen an die Produktionsprozesse reagieren.
Schnellere Umsetzung der Formatverstellung zur Kostenreduktion
Der Effekt der Kostenreduktion durch die Optimierung der Geschwindigkeit bei den Rüstzeiten macht sich am stärksten bei überwachter und vollautomatischer Formatverstellung bemerkbar.
Wenn bei der überwachten Formatverstellung bereits direkt an der Achse der einzustellende Wert über die Maschinensteuerung angezeigt wird, erübrigt sich für den Maschinenbediener die Recherche der Werte in hinterlegten Produktlisten. Noch effizienter ist die vollautomatische Formatverstellung, wenn keine Kurbel manuell bedient werden muss, sondern ein Positionierantrieb die Positionierung „per Knopfdruck“ übernimmt.
Erhöhte Genauigkeit zur Qualitätssteigerung bzw. -sicherung
Für die Einstellung einer bestimmten Position einer Achse ist zunächst ein möglichst genaues Messsystem vonnöten, mit dem sich bestimmen lässt, an welcher Position sich das Aggregat aktuell befindet. Bei der händischen Verstellung können jedoch Fehler auftreten und das Produktergebnis negativ beeinflussen. Im schlimmsten Fall könnte Ausschuss produziert werden, bis eine falsche Maschineneinstellung auffällt. Mit der Optimierung der Formatverstellung soll zudem die Wiederholgenauigkeit erhöht werden. Ein Produkt soll nach einem Wechsel auch bei erneuter Herstellung wieder in gleicher Form und Qualität vorliegen. Die Reproduzierbarkeit ist also ein entscheidender Faktor bei der Formatverstellung, damit eine konstante Produktqualität gewährleistet ist.
Erhöhte Prozesssicherheit durch Überwachung der Formate
Neben Reproduzierbarkeit und Kostenreduktion durch Geschwindigkeit ist eine Erhöhung der Prozesssicherheit ein weiteres Argument für eine Optimierung der Formatverstellung. Bei der überwachten Formatverstellung wird durch LED-Leuchten ein klarer Positionsstatus angezeigt, Grün bedeutet „Position korrekt“, Rot signalisiert „Position nicht korrekt“. Dies ist ergonomisch für den Bediener, und, was noch wichtiger ist, auslesbar für die übergeordnete Maschinensteuerung.
Damit besteht die Möglichkeit, die Maschine so zu programmieren, dass sie erst dann die Produktion wieder aufnimmt, wenn alle Positionen nach der Formatverstellung korrekt eingestellt sind. Entscheidend ist die Busfähigkeit der Positionsanzeigen, damit die Maschinensteuerung die Positionswerte auslesen und überwachen kann. Dank der Busfähigkeit bekommt die Maschinensteuerung die Ist-Werte von der Positionsanzeige übermittelt (Lesen) und kann wiederum ihrerseits die Soll-Werte vorgeben (Schreiben).
Mehr zum Thema intelligente Formatverstellung
Lesen Sie unseren umfangreichen Whitepaper Formatverstellung (PDF, 30 Seiten) in den Sprachen Deutsch, Englisch oder Italienisch.
Manuelle Formatverstellung mit Positionsanzeigen
Die manuelle Formatverstellung als einfachste und günstigste Variante ist prädestiniert für Basismaschinen mit seltenen Formatverstellungen. Es kommen mechanisch-digitale oder elektronische Positionsanzeigen zum Einsatz, die preiswert und zuverlässig die Positionierung feststellen. Innerhalb der Prozesskette „Metallumformung“ sind DAs für die Ausrichtung der Werkzeuge zuständig.
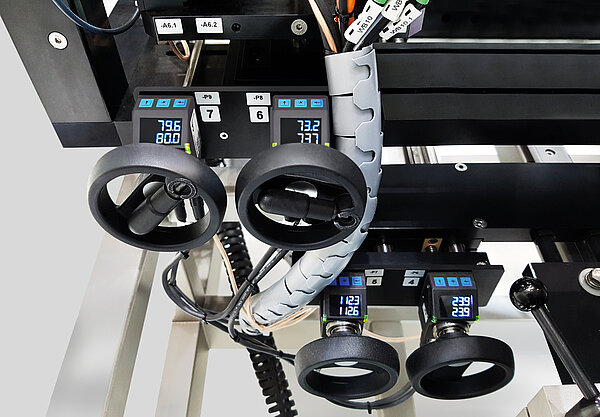
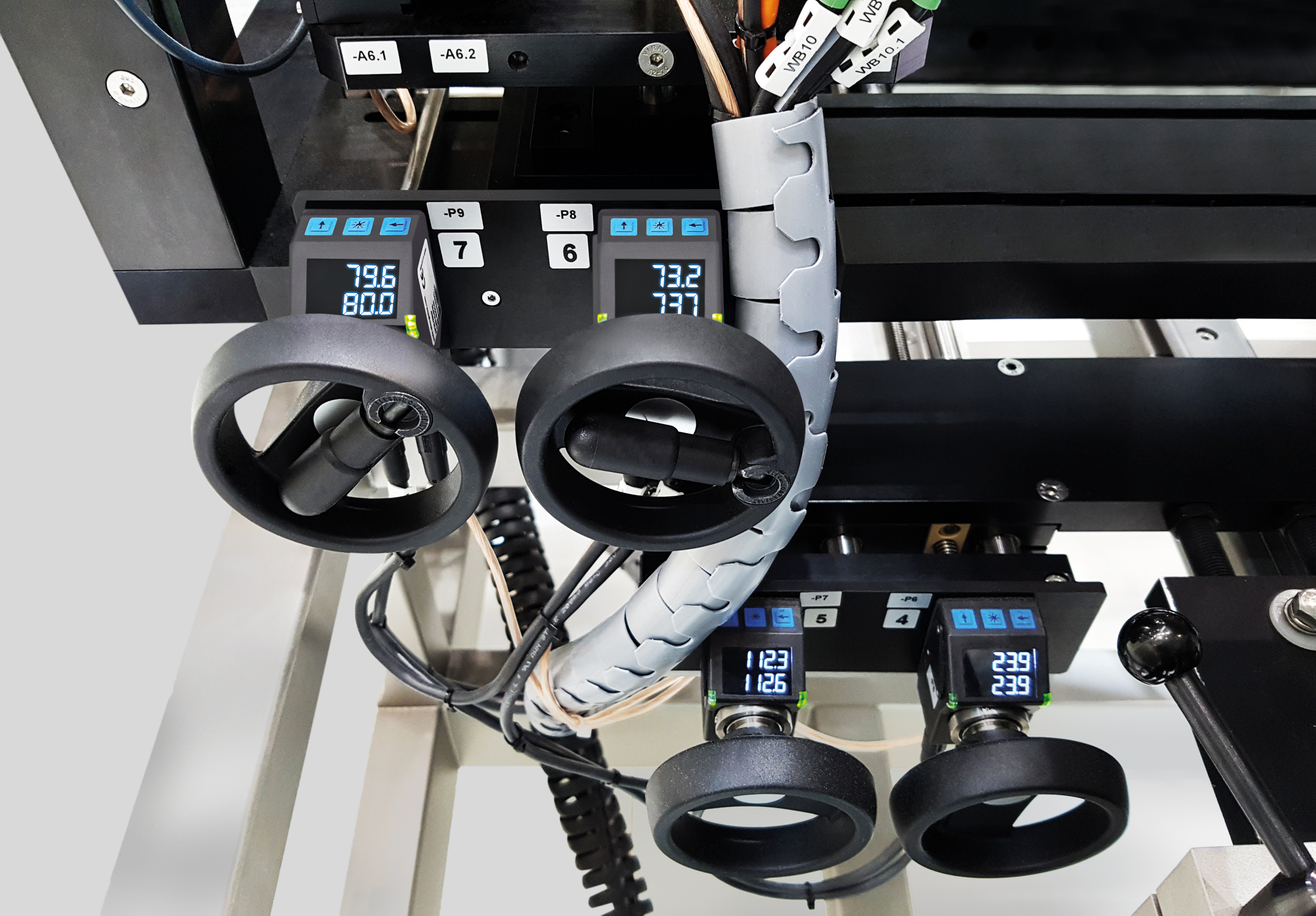
Grundanforderungen für Reproduzierbarkeit in der Formatverstellung
Die aktuelle Position einer Spindel muss zunächst einmal mit einem geeigneten Messsystem in einer definierten Genauigkeit gemessen werden können. Darüber hinaus muss für die Reproduzierbarkeit die Ist-Position in Klarwerten ablesbar sein. Grundsätzlich sind dies auch die Basisanforderungen bei der Formatverstellung über Schieber oder auch beim Formatteilwechsel. Die Formatteile müssen eindeutig gekennzeichnet sein, um sicherzustellen, dass der Bediener stets die gleichen, geforderten wieder einlegt.
Grundfunktionen und Aufbau von Positionsanzeigen
In jeder Positionsanzeige befindet sich ein Messsystem, das über eine hohe Genauigkeit verfügt, typischerweise mit einer Toleranz von ca. ±0.5 Grad. Außerdem bietet eine Positionsanzeige kontrollierbare digitale Anzeigewerte. Dabei sind unterschiedliche Anzeigewerte möglich, je nach entsprechender Spindelsteigung. In der Regel wird die Drehbewegung der Spindel in eine Linearbewegung umgesetzt, die einen Schlitten einstellt.
Die Spindelsteigung sagt dabei aus, welcher Weg pro Umdrehung linear durchgeführt wird. Entscheidend für die problemlose und kosteneffiziente Nachrüstbarkeit der Positionsanzeigen ist die Montage über eine Hohlwelle. Zudem ist die Positionsanzeige mit einem Gleitlager mit Lebensdauerschmierung ausgestattet, d. h. die Anzeige ist vollkommen wartungsfrei. Neben dem Messsystem beinhaltet eine Positionsanzeige auch ein Anzeigedisplay. Eine Variante sind die mechanisch-digitalen Positionsanzeigen, die sogenannten SIKO-Zähler, die die Werte in Dezimalstellen in Zehnerpotenzen in Form von Zahlenrollen darstellen. Elektronische Positionsanzeigen dagegen verfügen über ein LCD-Display.
Die AP-Serie für die überwachte Formatverstellung weist ebenso den Soll-Wert in der zweiten Anzeigezeile aus.
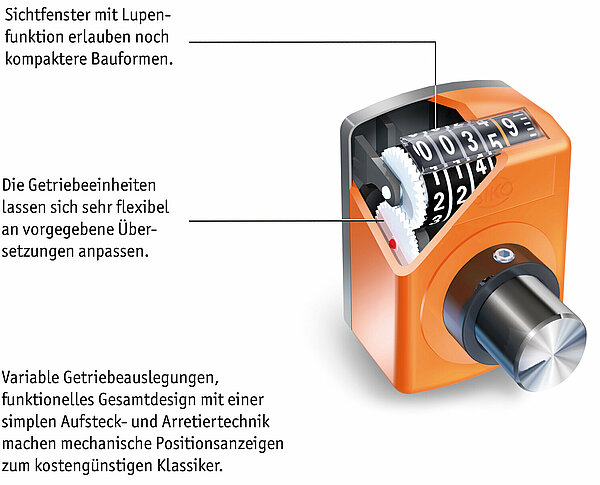
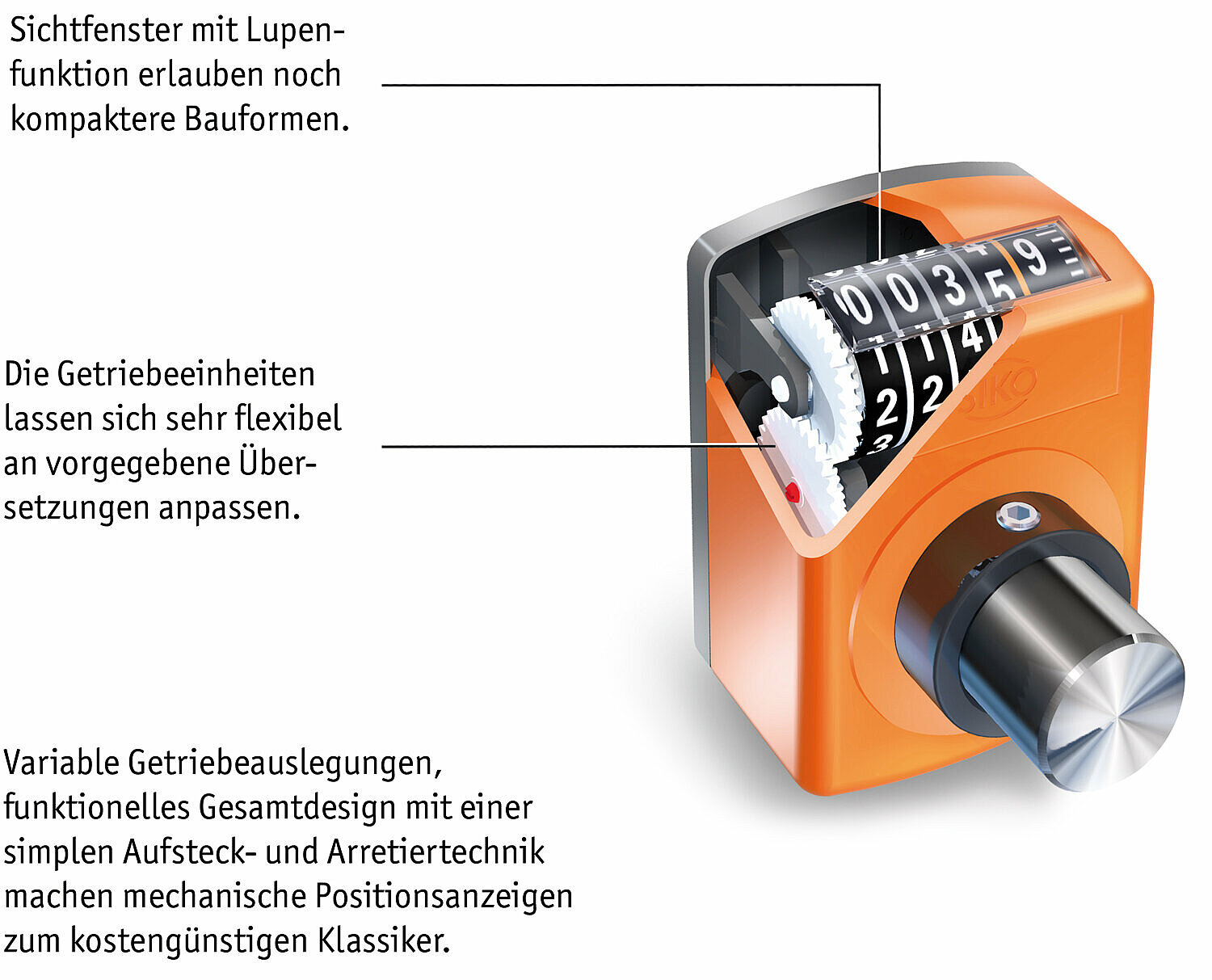
Kompakte Positionierantriebe zur einfachen Automatisierung vorhandener Verstellachsen
Grundlegender Aufbau eines Positionierantriebs: Die grundlegende Idee eines Positionierantriebs ist die hochintegrierte Bauweise inklusive des bürstenlosen Gleichstrommotors (der verschleißfrei ist), eines spielarmen und leistungsstarken Getriebes sowie der Positionsgeber und Leistungs-und Steuerungselektronik.
So kann der Positionierantrieb direkt mit der Steuerung verbunden werden. Auch der Positionierantrieb ist durch die integrierte Hohlwelle einfach an die vorhandene Spindel zu adaptieren.
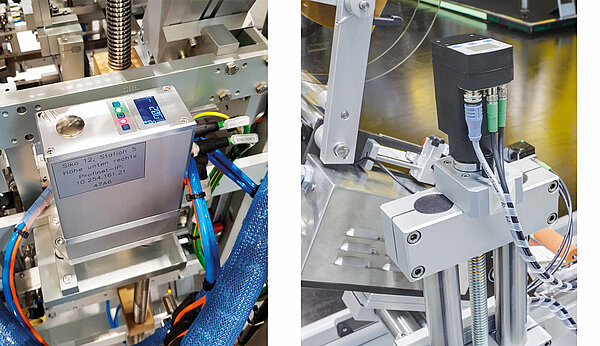
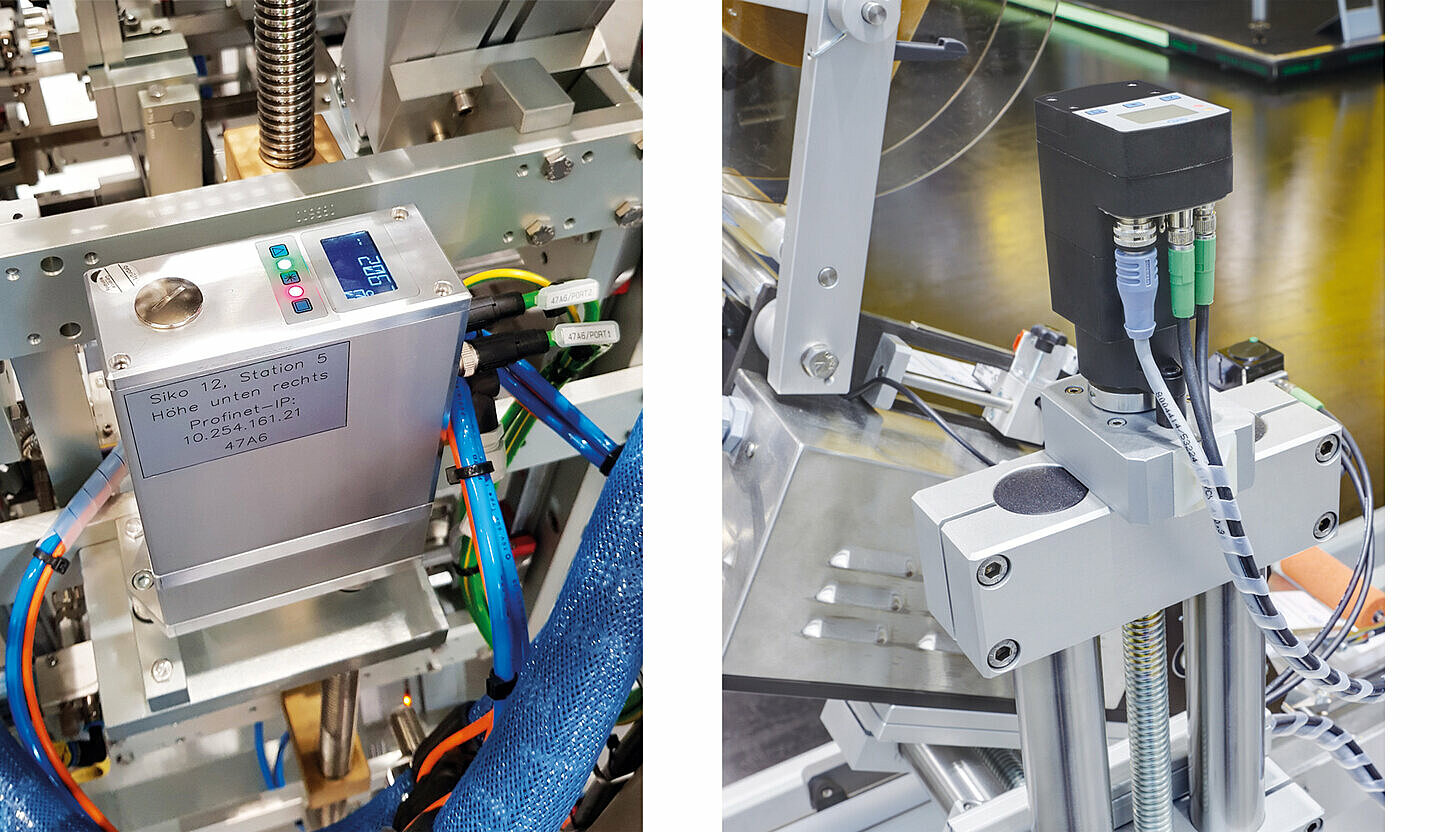
Wodurch sich der Antrieb insbesondere auszeichnet, ist die kompakte Bauweise mit hoher Leistung und zahlreichen Funktionen. Durch diverse Standardschnittstellen ist eine direkte Kommunikation mit der übergeordneten Maschinensteuerung (SPS) möglich. Die Regelung der vollautomatisierten Positionierung hinsichtlich u. a. Zielwert und Geschwindigkeit erfolgt jedoch innerhalb des Antriebs. Die sogenannten Prozessdaten, also Position, Geschwindigkeit, Drehrichtung werden dann kontinuierlich bereitgestellt und können auch von der Steuerung ausgelesen werden - wichtig für Überwachung und Diagnosemöglichkeiten.
Stellmotor und Software-Tools als Gesamtlösung zur Integration
Zusätzlich zum Stellmotor als Hardware an sich bietet SIKO diverse Software-Tools als Gesamtlösung an, die zur Diagnose oder zur vereinfachten Integration verwendet werden können. Zum Beispiel können einzelne Software-Treiber in eine Steuerung geladen werden, durch die ein Antrieb einfach zu identifizieren und letztendlich in das bestehende System zu integrieren ist.
Funktionsbeschreibung Positionierantrieb - Prozessdatenaustausch Soll-Wert, Ist-Wert, Geschwindigkeit
Die Positionierantriebe arbeiten prinzipiell in zwei verschiedenen Modi, die im Markt als Standardbetriebsarten gelten: Positioniermodus und Drehzahlmodus. Beim Positioniermodus wird der Soll-Wert von der Steuerung an den Antrieb übertragen und bei Bedarf in dem Zusammenhang auch noch der Ist-Wert von der Steuerung ausgelesen. Letzteres ist nicht zwingend notwendig, da der Ist-Wert auch direkt vom Antrieb überwacht wird. Der Antrieb regelt dann selbstständig mit der vorab von der Steuerung geforderten Geschwindigkeit in die gewünschte Position, bis er dort ankommt.
Der Positioniermodus ist die klassische Anwendung, während der Drehzahlmodus nicht ganz so verbreitet ist. Er eignet sich aber zum Beispiel dann besonders, wenn mehrere Achsen synchron gefahren werden sollen und in Echtzeit überwacht wird, dass alle Antriebe oder alle Achsen die gleiche Höhe oder die gleiche Position zu einem gewissen Zeitpunkt haben. Dies ist auch dann wichtig, wenn die Achsen zusätzlich noch mechanisch miteinander verbunden sind.
Beim Drehzahlmodus gibt die Steuerung nur eine Geschwindigkeit und Richtung vor und überwacht dann permanent den Ist-Wert, bis die gewünschte Position erreicht ist. Wenn der Antrieb in die Nähe der Position kommt, regelt die Steuerung die Geschwindigkeit bzw. die Drehzahl herunter. Eine wichtige Sicherungsfunktion ist, dass die Maschine erst dann wieder funktioniert, wenn alle Achsen bzw. Antriebe ihre jeweilige Position gefunden haben. Wenn die Position erreicht ist, dann wird im Telegramm – dem Kommunikationsaustausch zur Steuerung – ein entsprechendes Bit als Bestätigung der Position gesetzt. Zusätzlich könnte die Steuerung auch noch den Ist-Wert am Antrieb zurücklesen und erneut mit dem Soll-Wert abgleichen. Stimmen sie überein, kann die Steuerung die Wiederaufnahme der Produktion veranlassen.
Predictive Maintenance – Überwachung der Diagnosewerte Strom, Temperatur, Spannung
Hinter diesem Aspekt verbirgt sich die Diagnosefähigkeit der Positionierantriebe. Über diverse Anzeigewerte des Antriebs lassen sich Rückschlüsse auf den Betriebszustand sowohl des Antriebs als auch der Anlage an sich ziehen, um so frühzeitig Wartungsbedarf zu erkennen.
Beispielsweise lässt sich permanent die Stromaufnahme im Motor überwachen. Wenn deutlich wird, dass der Strom über einen gewissen Zeitraum kontinuierlich ansteigt, obwohl die Belastung an der Achse immer die gleiche ist, muss die Anlage überprüft werden.
Der Strom lässt sich auch in Verbindung mit der Temperatur, die direkt im Gerät ausgelesen werden kann, überwachen. Wenn die Temperatur ansteigt, ist die Belastung des Antriebs höher als üblich. Ursache kann die Umgebungstemperatur direkt am Antrieb sein. Zusätzlich ist es möglich, die Spannungswerte an Steuer- und Laststromkreis zu kontrollieren. Wenn Spannungsverluste auftreten, wenn der Antrieb nicht mehr 24 Volt am Laststromkreis oder am Steuerstromkreis aufweist, kann das ein Indikator dafür sein, dass die Netzversorgung nicht mehr die erforderliche Qualität erbringt.
Integration in Maschinensteuerungen (SPS) - Anforderungen und verfügbare Schnittstellen
Die Anforderungen zur Netzwerkintegration an die möglichen Schnittstellen betreffen zum einen die Applikation, z. B. die Reaktionsgeschwindigkeit in der Kommunikation. Zum anderen gibt es Anforderungen im Hinblick auf die Integration in die Maschine. Dazu zählt die Netzwerktopologie.Ersteres betrifft die Real-Time-Kommunikation, die bei der Automation für bestimmte Regelungen oder synchronisierte Bewegungen erforderlich ist. Werden also busfähige elektronische Positionsanzeigen als Feedback-Sensor für eine Automation genutzt, besteht hier eine Real-Time-Anforderung.
Bei der manuellen Formatverstellung dagegen sind Informations-Geschwindigkeiten von einigen Millisekunden bis zu einer Sekunde meist ausreichend und eine RealTime-Kommunikation somit unnötig. Die SIKO-Positionierantriebe sind zwar ebenfalls automatisiert, jedoch haben sie eine interne Regelung; sie bieten einen sogenannten Closed Loop. Durch diesen internen Soll-/Ist-Wert-Abgleich und den Positioniermodus ist eine millisekundengenaue Überwachung nicht notwendig. Die andere Anforderungsebene betrifft die Einfachheit und Betriebssicherheit der Netzwerktopologie, um die Geräte optimal in die Maschine integrieren zu können.
Die Netzwerktopologie kann ring-, stern- oder kettenförmig sein mit jeweiligen Vor- und Nachteilen. Darüber hinaus ist eine gewisse Kompatibilität gefordert, wenn in der Maschine bereits eine bestimmte Maschinensteuerung eingesetzt ist. Bei einer Siemens-Steuerung beispielsweise ist es am einfachsten, ein Gerät mit Profibus- oder Profinet-Schnittstelle zu integrieren.
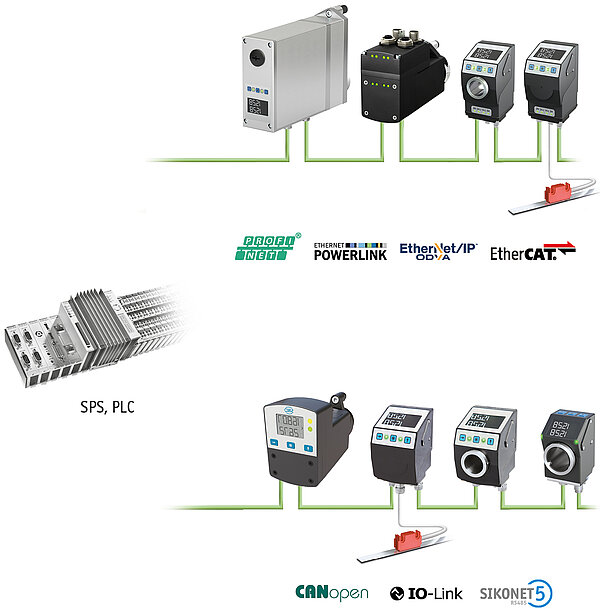
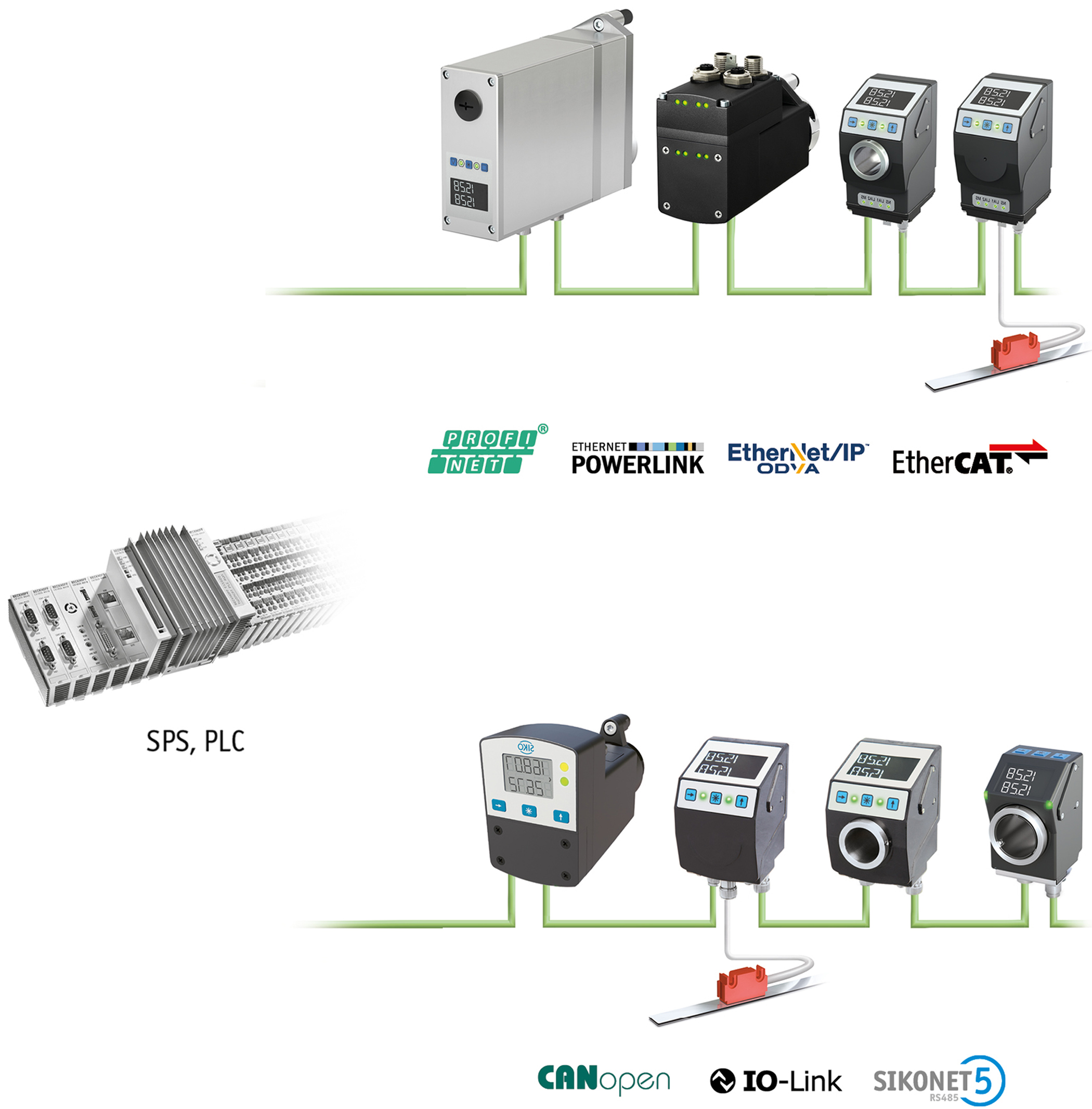
Retrofit mit vorprogrammierter HMI-Steuerung
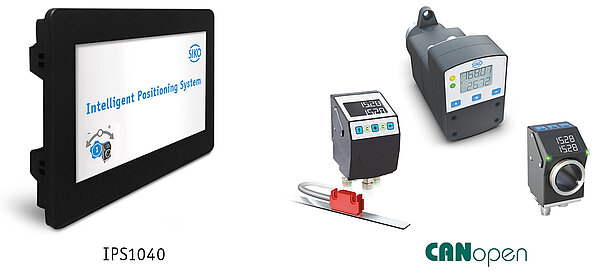
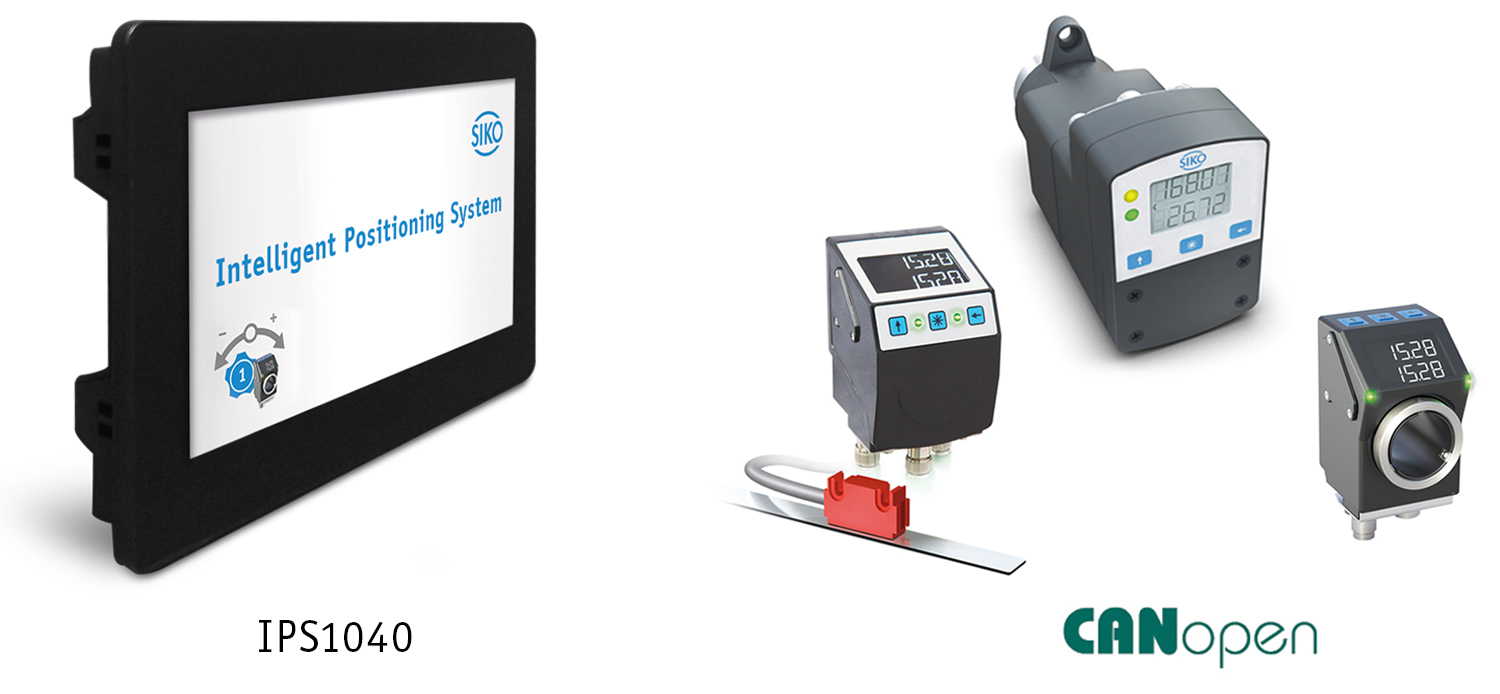
Häufige Verstellungen an älteren Produktionsanlagen ohne Maschinensteuerung können mithilfe der HMI-Steuerung IPS1040 als Retrofit-Lösung einfach optimiert werden, d. h. sowohl als überwachte Formatverstellung als auch komplett automatisiert. Es ist keine kostenintensive Umrüstung auf eine SPS nötig, sondern das IPS1040 verspricht eine schnelle Inbetriebnahme durch eine betriebsbereite Bedienoberfläche.
Über ein voraufgesetztes Programm können alle SIKO-Geräte im Bereich intelligenter Formatverstellung per Touch-Bedienung über das Display parametriert werden. Im laufenden Betrieb kann damit eine Vielzahl von Rezepten für verschiedene Produkte vorgegeben werden, die in einer Rezeptverwaltung hinterlegt sind.
Sie lassen sich durch den Bediener über das Display anwählen. Automatisch werden dann Soll-Werte an alle Achsen oder Linearverstellpositionen gesendet, die vom Positionierantrieb automatisch angefahren oder eben manuell verstellt und mit einer elektronischen Positionsanzeige überwacht werden können. Der Automatisierungsgrad der Maschine ist dabei individuell zu bestimmen.
Bei Achsen, die sehr häufig verstellt werden müssen, empfiehlt sich die automatisierte Variante durch einen Positionierantrieb. Verstellpunkte dagegen, die seltener verändert werden müssen, können mit einer elektronischen Positionsanzeige überwacht werden.
Ausblick: Relevanz intelligenter Formatverstellung für die Zukunft
Der Trend zur Individualisierung von Produkten und damit verbunden die Erforderlichkeit einer flexiblen, intelligenten Formatverstellung werden anhalten oder vermutlich weiter zunehmen. Das Schlagwort „One-Piece-Flow“ ist dabei entscheidend. Die Maschine muss eine solche Flexibilität bieten, dass sie auch die Stückzahl „eins“ fertigen kann, ohne die Kosten dadurch exorbitant in die Höhe zu treiben.
Der Anspruch an individualisierte Produkte steigt, zurechtgeschneidert für den Kunden – ob im Industrie- oder im Consumerbereich. Mehr Individualität bei den Produkten erfordert auch höhere Flexibilität im Maschinenbau. Der Automatisierungsgrad in den Maschinen wird dadurch sicher eher noch weiter zunehmen, als dass er geringer wird.
Letztendlich geht es auch darum, eine schnelle Anpassung an die Marktbedingungen zu ermöglichen, sodass beispielsweise Aktionsware schnell und kosteneffizient produziert werden kann, z. B. im Supermarkt und im Getränkebereich. Im Gebinde könnte eine Flasche mehr gewünscht sein oder statt eines Inhalts von 0.33 Litern sollen nun 0.5 Liter gefüllt werden.
Auf herrschende Marktbedingungen müssen Maschinen also flexibel einstellbar sein. Auch ein schnellerer Durchlauf ist hierbei vonnöten. Das Thema Kostenreduzierung ist in der Produktion zentral, beispielsweise durch deutlich verminderte Umrüstzeiten ganzer Produktionslinien bei immer häufigeren Produktwechseln.
Ein weiterer Aspekt ist die Sicherheit bei der Formatverstellung, der eine immer höhere Bedeutung zukommen wird. Dazu gehört es, Prozesse nachzuvollziehen, die Richtigkeit der Einstellungen zu gewährleisten. Eine überwachte oder automatisierte Formatverstellung ist für die Überwachung und Gewährleistung der Prozesse in der Zukunft unabdinglich.
Die Fehleranfälligkeit durch den „Faktor Mensch“ kann hierdurch weiter reduziert werden, da der Bediener nicht mehr die eigentliche Verstellung zu verantworten hat, sondern vieles wird automatisch von der Maschine geleistet. Der Anspruch an das Bedienpersonal sinkt damit.
Mehr zum Thema intelligente Formatverstellung
Lesen Sie unseren umfangreichen Whitepaper Formatverstellung (PDF, 30 Seiten) in den Sprachen Deutsch, Englisch oder Italienisch.
Verfügbare Flyer zu der Thematik
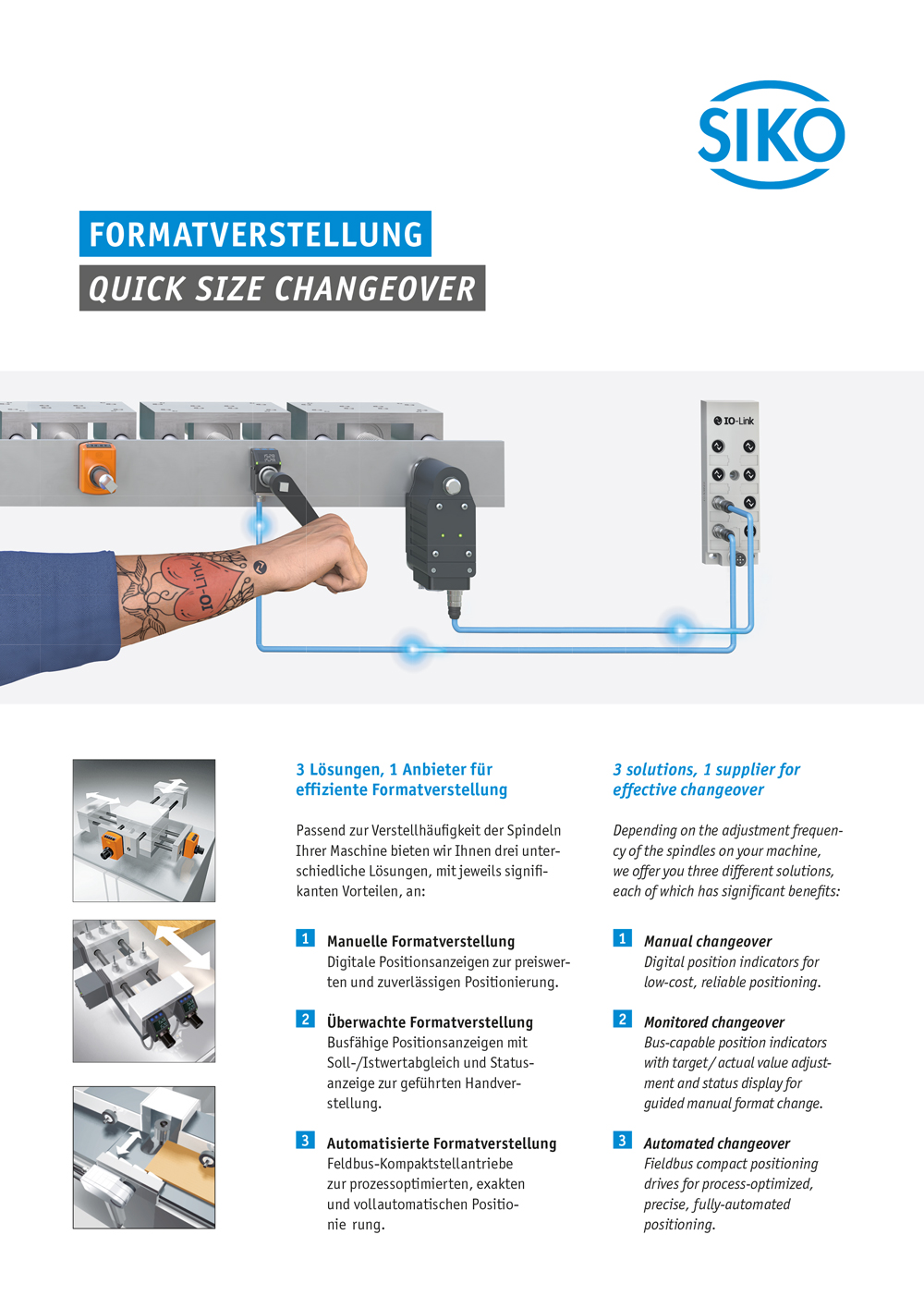
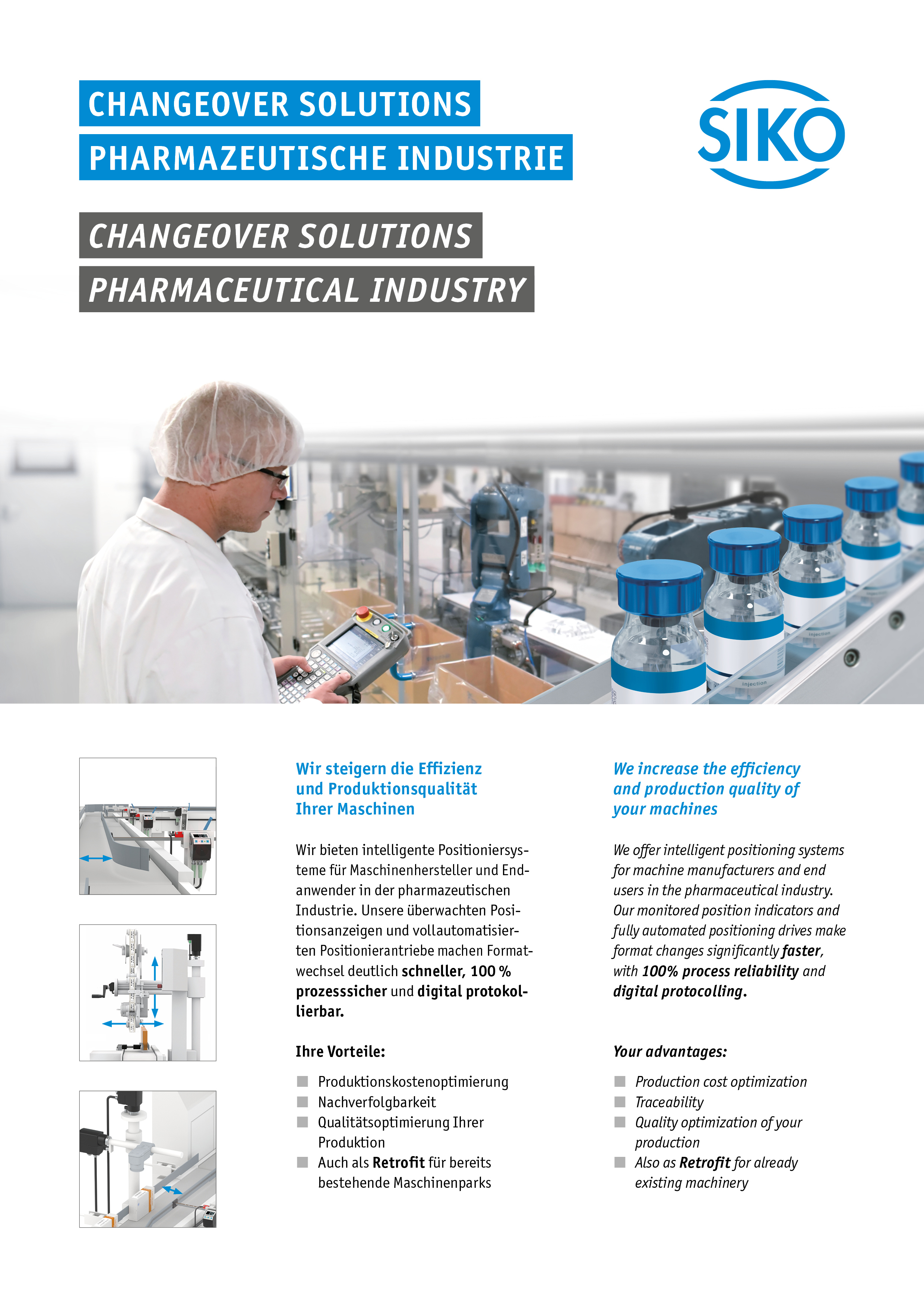
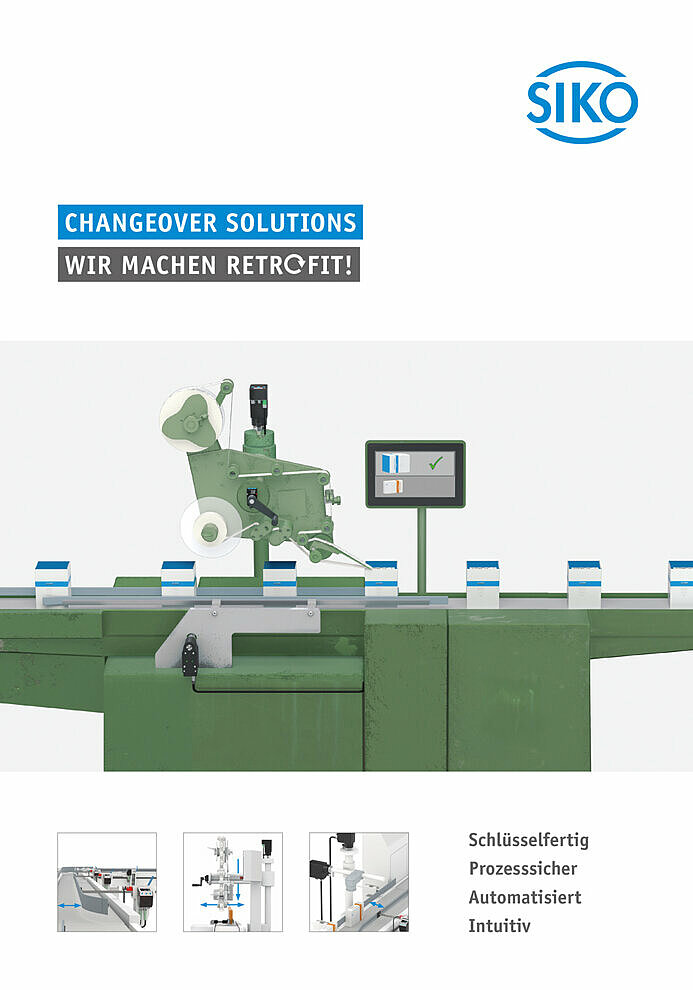